Why is the strength of HDPE pipes a vital concept to explore? Here we will help illustrate the role of HDPE pipes in creating infrastructure for a sustainable future, describe the strength properties of HDPE pipes and dispel the misconception that HDPE pipes are not durable or suitable for pressure-rated applications, explore typical applications, and highlight HDPE pipe performance through recent case studies.
Water and Wastewater Infrastructure for a Sustainable Future
Water infrastructure has always been essential to the advancement and development of human civilizations, with the greatest civilizations immortalized in history for their ability to bring water and food to the masses. As civilizations developed larger, more complex cities, water infrastructure evolved from clay pipes and concrete aqueducts to high-density polyethylene (HDPE) pipes and enclosed canals (1). Each developmental step focused on overcoming new challenges.
Today, the challenge is clear: America must fix its aging water infrastructure. The problem costs the country billions of dollars in water loss from leakage and sewer infrastructure damage from corrosion, and it isn’t an easy fix. One complication with water and wastewater infrastructure repair is how and where these pipes were installed. For years, water and sewer lines were installed under streets and roadways in cities. This approach has created two problems: traffic issues during repairs and costly roadway damage by broken or leaking lines.
With their unique properties, HDPE pipes have fundamentally reshaped how we can develop water infrastructure (2). They are strong and robust enough to support solid-walled pressure pipe applications while being flexible enough to be installed through trenchless means such as horizontal directional drilling (HDD). HDD is especially important as it allows cities to bypass many issues related to pipeline repair for lines installed under roadways.
HDPE pipes are a game changer across various industries, from mining and agriculture to water and gas distribution, thanks to their remarkable adaptability and resistance to corrosion, abrasion, and high impacts (3, 4).
Properties Demonstrating the Strength of HDPE Pipes
HDPE pipes are available as solid-walled pressure pipes. The pipe’s pressure rating depends on the wall thickness compared with its outer diameter—the Standard Dimensional Ratio (SDR). The lower the ratio, the thicker the pipe is in relation to its outer diameter and the higher its pressure rating. HDPE pipes are certified to serve as pressure pipes according to AWWA C906-21, with pipes capable of reaching SDR 9 and lower.
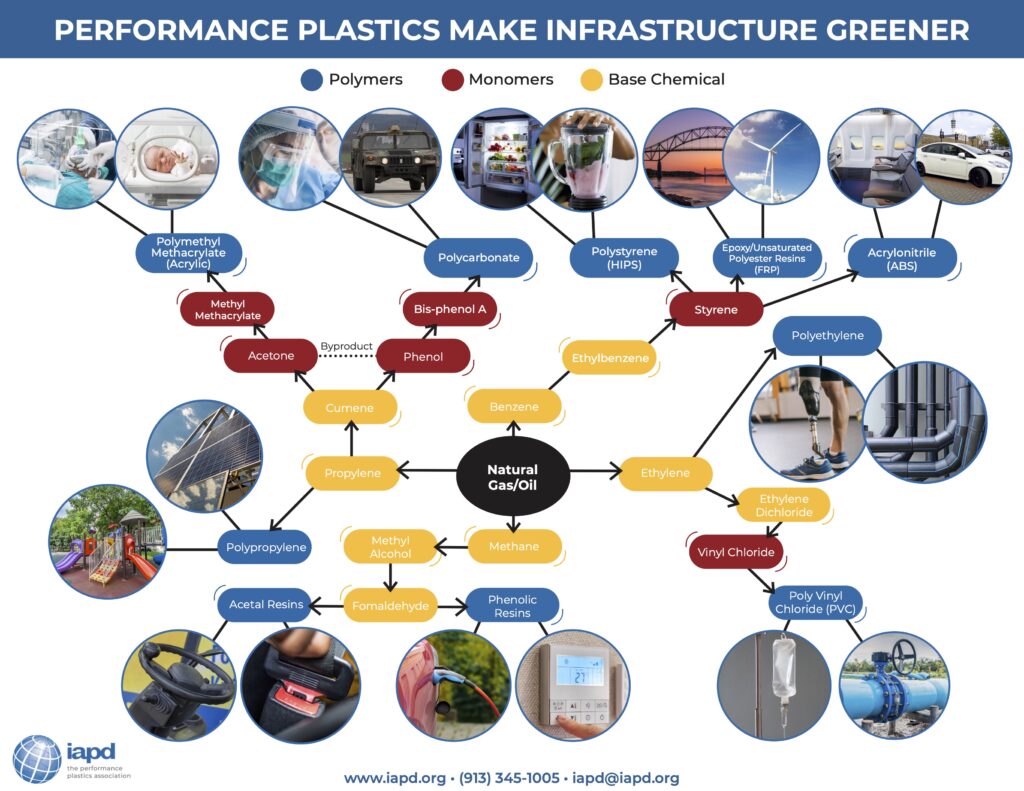
From a design perspective, pipes are classified as either rigid or flexible. Rigid pipes are designed to be more rigid than their surrounding soil and withstand the applied loads by their inherent strength. In contrast, flexible pipes rely on the surrounding soil’s capacity to carry a substantial portion of the applied load via ring deformation, activating the soil’s lateral passive resistance (5). HDPE pipes, even those with thicker walls, are flexible because of the material’s mechanical characteristics such as a relatively high strain rate. As a result, an HDPE pipe’s structural integrity is based on pipe stiffness, meaning that an HDPE pipe deflects under soil weight and produces passive soil support at its sides (6).
HDPE pipes also offer great tensile strength, allowing them to bear both short-term and long-term pulls or impacts, enhancing their durability and longevity. This point has already been reported in the literature where HDPE pipe specimens showed no significant alterations in tensile strength even after a year of exposure to varying environments, such as acidic, alkaline, freeze-thaw cycles, and saline solutions, as shown in Figure 2 (7).
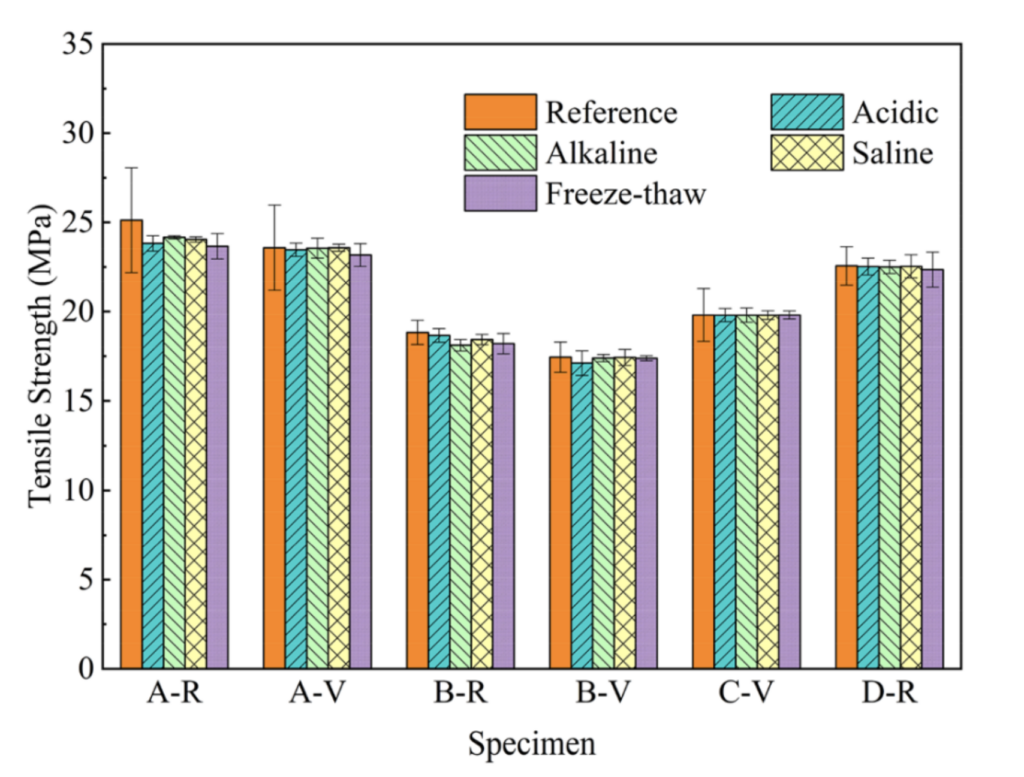
Another significant aspect contributing to the strength of HDPE pipes is their slow crack growth resistance (1). This quality ensures an extended lifespan of the pipes by effectively resisting crack propagation over time. This feature is vital in preventing sudden and unforeseen failures that could lead to considerable damage. The temperature-dependent stress-strain behavior of HDPE pipes, Figure 3, indicates a ductile fracture across all temperature ranges (8). This ensures that the material deforms under stress before breaking and further underscores the ability of HDPE pipes to maintain their structural integrity under different conditions.
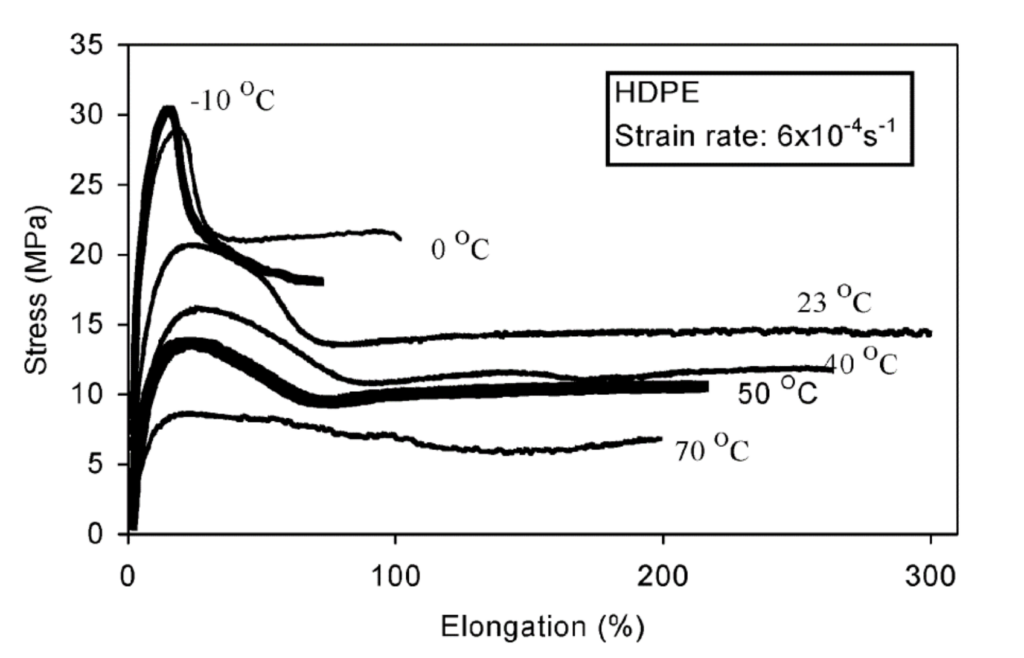
A previous study has indicated that the strength of HDPE pipes exhibits lesser temperature dependence than PVC and CPVC pipes (8). This means that the yield strength of HDPE decreases at a slower rate than PVC and CPVC with varying temperatures, signifying that temperature variation has a limited effect on the yield strain of HDPE, thus maintaining its strength over a more comprehensive temperature range.
In addition to their strength characteristics, HDPE pipes display unique properties such as flexibility and resistance to abrasion and corrosion, including those induced by electrochemical-based processes (9). This advantage results in long-term smooth surfaces, consistent flow rates, lower pumping energy consumption, and reduced susceptibility to biological growth and other forms of fouling (10, 11). It is noteworthy that HDPE pipes can be produced from PE100-RC composite material, which adds durability and strength to the system.
Applications Best Suited for HDPE Pipes
HDPE pipes’ mechanical properties, durability, and ease of installation make them suitable for various construction and installation procedures, including the trenchless construction method that involves drilling along a predetermined path and installing the HDPE pipe (12, 13).
One of the most significant applications of HDPE pipes is in the water and wastewater industry (14). HDPE pipes are ideal for transporting potable water due to their non-corrosive nature. In contrast, traditional pipes, such as those made from iron or steel, are prone to rusting, which can contaminate the water supply (15). Moreover, HDPE pipes can withstand the harsh chemical environment in wastewater systems, demonstrating excellent resistance to a broad spectrum of aggressive chemicals.
HDPE pipes are also used in gas distribution networks. When properly installed, their leak-free joints and resistance to slow crack growth significantly reduce the risk of gas leakage, making them safer for gas transportation (2). On the other hand, HDPE pipes are adopted in the mining industry due to their robustness and durability, where their high impact resistance allows them to handle the abrasive materials commonly found in mining applications.
The agricultural sector has seen an enormous increase in the use of HDPE pipes. They are often used for irrigation systems because they are weather-resistant and can handle fluctuating temperatures (16). Their ability to resist root intrusion also makes them ideal for subsurface installation. HDPE pipes also find application in the telecom industry, using them as conduit pipes for optical fiber cables. They provide excellent protection to the cables due to their high crush resistance.
Additionally, their flexibility allows them to be installed in diverse terrains and conditions. For example, HDPE pipes are used for stormwater drainage systems (1). Their lightweight and easy-to-install nature make them more cost-effective and efficient than traditional materials.
HDPE Pipe Performance
This section discusses two large-scale projects to explore the applications and performance of HDPE pipes.
The first case is Mobile, Alabama’s Three Mile Creek Trunk sewer upgrade project. The project was a significant sewer upgrade to replace existing 36” and 42” diameter trunk sewers with an 11,000 ft, 60” diameter gravity trunk sewer main. This upgrade bolstered transmission and storage capacity, reducing sanitary sewer overflows during rain events.
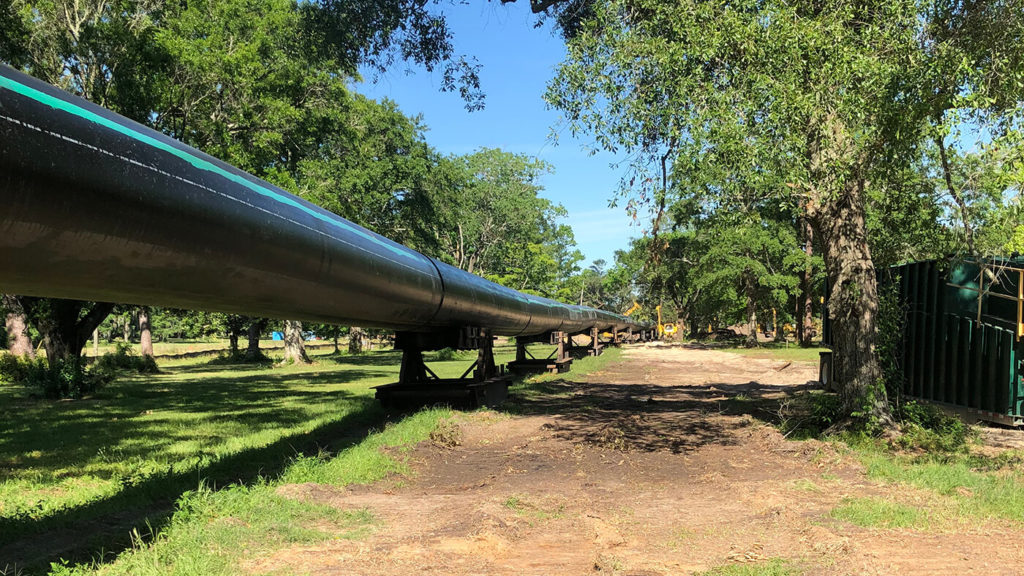
The project’s primary design challenge was related to the installation sites’ large pipe size and construction constraints. The limited available working space and installation lengths posed significant issues. The engineering team utilized two sizes of AGRU’s HDPE pipes. The flexibility of these HDPE facilitated the installation, overcoming the site limitations.
The HDD technique was selected as the installation technique due to its effectiveness in such challenging scenarios. The design had to cater to the existing pipeline, portions of which could not accommodate larger diameters. This constraint necessitated using 48” and 63” diameter pipes with a standard dimension ratio (SDR) 11.
The project has seen significant time savings and success in pipe installation. HDPE pipes and HDD have negated the need for time-consuming tunneling beneath the creek. The project was one of North America’s largest diameter HDPE HDD projects, representing the HDPE pipes’ potential and performance capabilities.
The second project was a new sewer main for Fort Lauderdale. In 2020, Florida’s City Commission initiated a $65 million project to develop a 7.5-mile wastewater transmission line from Coral Ridge Country Club Wastewater Lift Station to the G. T. Lohmeyer Wastewater Treatment Plant. This project aimed to enhance the city’s infrastructure reliability while increasing redundancy and improving services.

The main challenge was that the route encompassed residential zones and public roadways, demanding a piping solution compatible with underground HDD. In this regard, the project team decided to use the 54” diameter HDPE pipes produced by AGRU due to their unique strength/weight ratio, flexibility, durability, corrosion resistance, and fewer mechanical joints, significantly reducing long-term maintenance requirements.
This piping system also improves resilience against rising sea levels and groundwater tables, aligning with the city’s more extensive climate adaptation strategies. The project was divided between Murphy Pipeline Contractors and David Mancini & Sons to expedite construction. Upon completion, the project set a global record for being one of the largest and longest HDD pressurized sewer pipe installations, with a notable achievement of 3,100 ft at 54” outside diameter. This entailed fusing approximately 23 pipe sections as it was being pulled. This case affirms the performance of HDPE pipes in large-scale infrastructure projects, demonstrating their strength for complex urban wastewater management.
Summary
The strength of HDPE pipes, flexibility, and corrosion resistance make them an exceptional choice for various applications. The performance of AGRU’s HDPE pipes, in particular, exemplifies the superior characteristics of these products, as demonstrated in various projects across the country. Whether upgrading sewer systems or constructing new ones, HDPE pipes consistently prove their resilience and reliability when properly installed. Their ability to endure high-pressure environments, withstand seismic activities, and resist corrosion underpins their strength and underscores their suitability for diverse applications.
Are you interested in learning about how you can leverage the benefits of HDPE pipes in your next project?
Contact Us
References
(1) K. Q. Nguyen et al. “Long-term testing methods for HDPE pipe-advantages and disadvantages: a review.” Engineering Fracture Mechanics. 2021.
(2) K. Peterson. “HDPE pipe for corrosion-and leak-free operation.” ASHRAE Journal. 2017.
(3) C. G. Rubeiz. “Case studies on the use of HDPE pipe for municipal and industrial projects in North America.” in Pipeline Engineering and Construction: What’s on the Horizon?. 2004.
(4) G. Scarascia-Mugnozza et al. “Plastic materials in European agriculture: actual use and perspectives.” Journal of Agricultural Engineering. 2011.
(5) J. Q. Zhao and S. Kuraoka. “Durability and Performance of Gravity Pipes: State-of-the-art Literature Review.” Institute for Research in Construction. 1998.
(6) ACPA. “Concrete or HDPE: Strength versus Stiffness.” American Concrete Pipe Association. 2004.
(7) K. Q. Nguyen et al. “Effects of Exposure Conditions on Antioxidant Depletion. Tensile Strength. and Creep Modulus of Corrugated HDPE Pipes Made With or Without Recycled Resins.” Journal of Polymers and the Environment. 2022.
(8) N. Merah et al. “Effect of temperature on tensile properties of HDPE pipe material.” Plastics. rubber and composites. 2006.
(9) G. DeCou and P. Davies. “Evaluation of abrasion resistance of pipe and pipe lining materials.” California Department of Transportation. 2007.
(10) IERE. “Life cycle assessment of PVC water and sewer pipe and comparative sustainability analysis of pipe materials.” Institute for Environmental Research & Education. USA. 2017.
(11) J. Rubulis and T. Juhna. “Evaluating the potential of biofilm control in water supply systems by removal of phosphorus from drinking water..” Water Science and Technology. 2007.
(12) M. Najafi. Trenchless technology piping: Installation and inspection. McGraw-Hill Education. 2010.
(13) M. P. Olson et al. “Jacking force and productivity analysis of pilot tube microtunneling installations.” Journal of Pipeline Systems Engineering and Practice. 2016.
(14) F. Du et al. “Life cycle analysis for water and wastewater pipe materials.” Journal of Environmental Engineering. 2013.
(15) A. H. Nielsen et al. “Influence of pipe material and surfaces on sulfide related odor and corrosion in sewers.” Water research. 2008.
(16) J. Qu et al. “Temperature and Water Quality on Migration of Total Organic Carbon from the High-Density Polyethylene Drip Irrigation Pipes.” Sensor Letters. 2012.
(17) F. R. Rofooei et al. “Parametric study of buried steel and high density polyethylene gas pipelines due to oblique-reverse faulting.” Canadian Journal of Civil Engineering. 2015.