You’ve just finished construction on a new manufacturing plant. Weeks go by and all seems well. Suddenly, you get a call. The plant was forced to shut down a production line due to a leak. One of the fabricated parts isn’t holding up. You order a replacement made from a stronger alloy. The call comes again several more times. By now you’ve exhausted most materials, but nothing seems capable of standing up to the extreme conditions at this step of the manufacturing process. What do you do?
You dig in and do a bit of research. One word keeps coming up: fluoropolymers. You do a bit more reading and find out that this is exactly what you need. But as you start looking through your options, you start to realize that the solution isn’t as easy as it seemed. There are more than a dozen types, each with various brands, grades, and ideal operating conditions. How do you choose the right fluoropolymer solution? In this article, we will discuss typical use cases for fluoropolymers, provide an overview of some typical options, and describe how you can leverage the Plastics Experts to help you determine the best solution for your use case.
What kind of problems can be solved with fluoropolymers?
Fluoropolymers are specialized materials that are rarely the first thing that anyone considers when they are designing an industrial manufacturing process. After all, these materials are not cheap. But when you’ve exhausted all other options, then a specialist is what you need. Fluoropolymers are polymers with multiple carbon–fluorine bonds, which contributes to its high resistance to solvents, acids, and bases. Furthermore, fluoropolymers resist most forms of corrosion and remain stable at temperatures that would melt other plastics. These combination of traits make them perfectly suited as a material in components exposed to extreme conditions.
There are also fluoropolymer grades that are made for high-purity applications.
What are the different types of fluoropolymers?
One way to classify fluoropolymers is to imagine that each type belongs to a different plateau on a step graph. The first few levels on the graph are occupied by semi-fluorinated polymers such as PVDF and ECTFE.
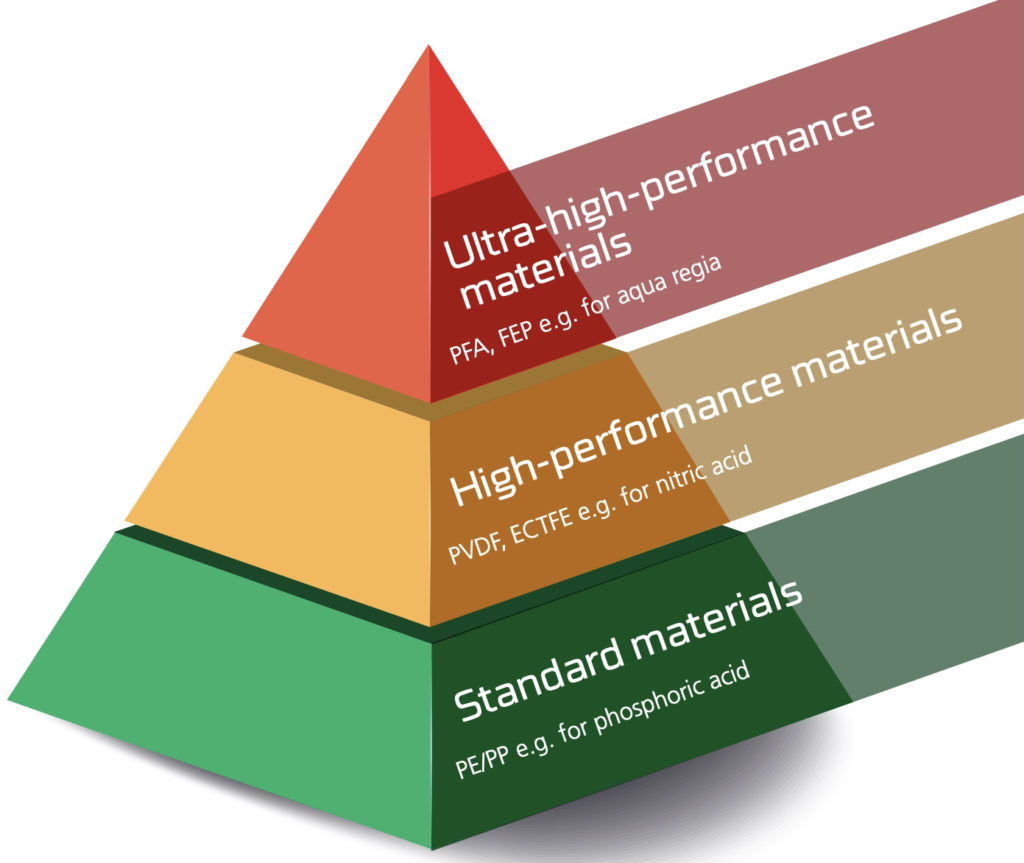
The first level is occupied by PVDF, which is thermally stable between -20°C and 150°C. It is important to keep in mind that the operating temperature for each fluoropolymer depends on the chemical media (and concentrations) that will come into contact with the material. Therefore, while PVDF is stable while in contact with 10% nitric acid at 80°C, its recommended operating temperature will decrease as the nitric acid concentration increases. Within PVDF there are also slight physical variations based on brand and grades. For example, flexible grade PVDF, which has increased flexibility and better stress cracking performance. However, while flexible grades may improve stress crack resistance, there is a trade off in some cases for lower maximum temperature performance, thus it is imperative to have an expert assist in the best solution. This principle applies to the other types of fluoropolymers.
ECTFE, also referred to as Halar®, is another semi-fluorinated polymer that operates at around the same upper limit as PVDF, but with a lower limit of around -70°C and a wider chemical compatibility. For example, ECTFE is resistant to bases and more solvents than PVDF. The next two steps are occupied by FEP and FPA, pure fluoropolymers. These materials are capable of operating at an even wider temperature range while also providing an expanded set of options in terms of media and concentrations they can contain. PFA, for instance, is chemically stable up to 260°C and is resistant to extreme corrosion from media like aqua regia.
PFA can also be used in high-purity applications, with the standard grade meeting purity requirements on an order of parts per million. There are also specialized high-purity PFA grades that can meet purity requirements on an order of parts per billion.
We hope this summary has highlighted an important aspect of fluoropolymers: When it comes to solutions, there is no shortage of options. But we know that between the various types, brands, grades, and operating conditions of fluoropolymers, choosing the right option can be daunting. But it doesn’t have to be. As the Plastics Experts, AGRU America is committed to helping you land on the right fluoropolymer for your needs.
How can The Plastics Experts help me choose the best solution?
When it comes to fluoropolymers, our process at AGRU is simple: Help provide customers with enough information to properly specify their project and their needs. What does that mean? From a product perspective, we provide guidance based on various brands and grades, with the goal of developing the broadest specifications possible. We also help clarify important distinctions, such as differentiating between sheet and piping grades. Finally, we provide guidance when it comes to fabricators, providing a list of great options as well as highlighting specialists who are better equipped for delivering components for certain applications.
How do you know you are in good hands? AGRU is an international manufacturer of thermoplastic semi-finished products such as sheet stock and rods, which have been used to create components for numerous applications. We have been in business for over 7 decades and have collected many case studies of our successes. In one case study, for example, our PFA sheets were used to create a lining to protect ventilation pipes that were failing in a chemical-processing facility and halting a production line every few months. The PFA lining solved the problem and allowed the facility to function without costly downtime.
Is it time to find a fluoropolymer to solve your unique challenge? Speak with the Plastics Experts to help find the right solution for you.
Contact