Polyethylene (PE) has helped revolutionize the piping industry by offering a long-term, safe, and efficient means for creating multipurpose pipes for gas, water, and wastewater applications. Case studies show PE pipes performing without problems for over 60 years. This level of performance, on top of its low leakage rates, resistance to biofouling and corrosion, and minimal maintenance requirements, have made it a material of choice for building robust piping systems. However, new advances in PE have led to creating a more robust resin that promises even better performance for modern piping systems.
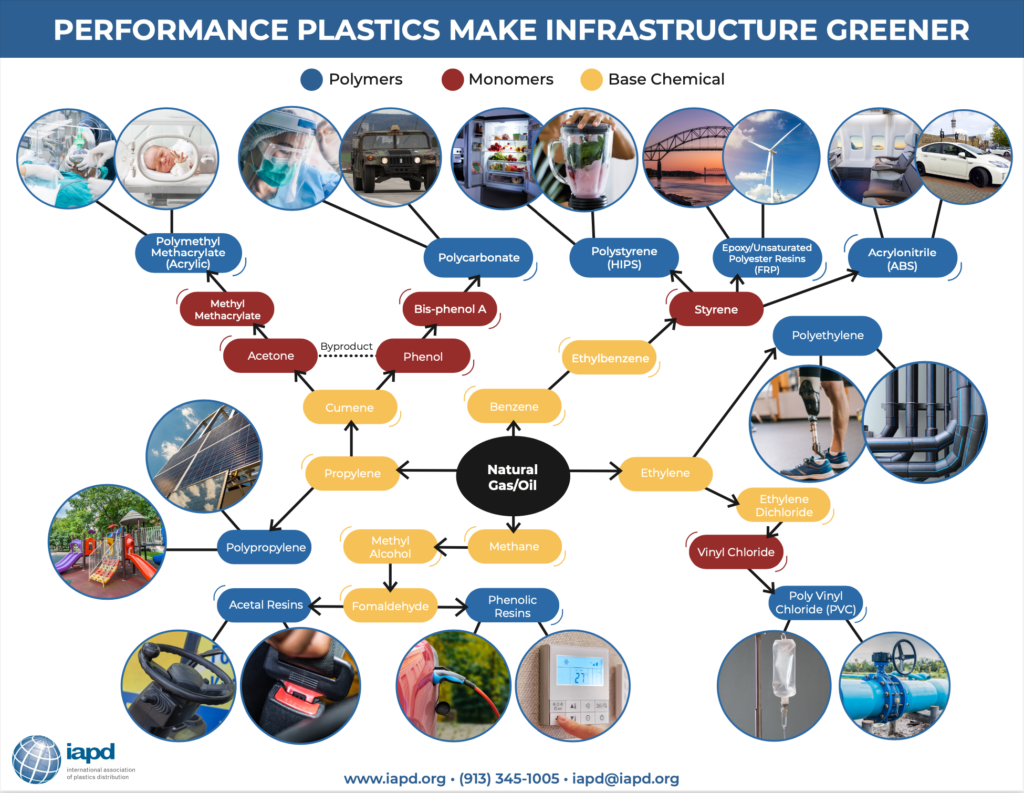
This article will describe the three stages of failure for PE pipes, explore the benefits of PE100-RC pipes and how it can help overcome a typical failure point experienced within long-term piping applications, and explain how to source the best PE100-RC pipes on the market.
Understanding long-term failure behavior of PE pipes
The most direct cause of failure for PE pipes is ductile deformation caused by high internal pressures and high hoop stresses. Failures of this nature are typically a design error or operational oversight that did not accurately account for the strains subjected to the pipe.
For long-term piping applications (>100 years) under typical loads, the limiting factor to PE pipes service life is slow crack initiation and slow crack growth (SCG). Eventually, PE pipes will reach the end of their service life when cracks form, leading to deformations—typically between 50 and 100 years, depending on typical operational stresses.
After SCG, the next cause of failure is thermo-oxidative aging, which leads to polymer degradation. For most applications, adding stabilizers to the resin is sufficient to keep the material intact throughout the service life of the pipes (1). See Table 1 for a summary of the failure behavior of PE pipes.
Table 1. Failure Behavior of PE Pipes (from reference 1).
Stage | Cause | Failure Point | Prevention |
Stage 1 | High internal pressures and high hoop stresses | Ductile deformation | Managing internal pressures and lowering hoop stress |
Stage 2 | Crack initiation and slow crack growth | Small-scale plastic deformation at crack tips | Controlling slow-crack growth |
Stage 3 | Thermo-oxidative aging | Polymer degradation | Incorporating stabilizers |
Most modern applications of PE pipes would have their service life limited by stage 2 failures caused by minor imperfections on the pipe that promote slow crack growth. Anything from regular operational stresses to slight damage during installation can serve as the starting point for cracks that eventually cause deformations after decades of service. To create piping systems using the latest trenchless methods that can withstand seismic activity and exceed a 100-year service life, look no further than PE100-RC.
The benefits of PE100-RC
PE100-RC pipes are recognized for their uses in trenchless applications, especially throughout Europe and the United Kingdom. While not prevalent in the United States, the piping material offers many unique advantages.
PE100-RC is a modified PE100 resin that offers enhanced resistance to slow crack growth. One of the most significant advantages of using PE100-RC pipes is preventing stage 2 PE pipe failures related to SCG, supporting a longer service life. Additionally, PE100-RC pipes are better suited for trenchless applications and piping systems in areas with seismic activity. The material also has the ability to be used in larger pipes for high-volume flow, which is especially useful for wastewater facility outfall pipes and stormwater applications.
Sourcing PE100-RC pipes and fittings from AGRU
AGRU manufactures PE100-RC pipes from its cutting-edge XXL pipe production facility at Charleston, SC, at sizes up to OD 3500 mm and 610 m in length. These pipes are suited for high-volume flow applications such as cooling water intakes for power plants, large sewage systems, seawater desalination, or mining operations. The ductility of PE100-RC pipes allows them to prevent stage 1 failures related to pressure surges and are available in a wide range of SDRs. Other benefits of the piping material include smooth internal surfaces that maximize flow capacity, lower pumping costs, reduce pitting and biofouling opportunities, and cut down on required maintenance.
Additionally, AGRU manufactures PE100-RC fittings for best interoperability. Installers can create “leak-free” joints using fusion welding to minimize leakage and significantly improve overall system performance.
Are you interested in learning more about how AGRU’s PE100-RC pipes and fittings can make a difference in your next project? Reach out to an AGRU representative today.
Reach Out
References
- 1. Frank et al., “Lifetime Prediction of PE100 And PE100-RC Pipes Based on Slow Crack Growth Resistance.” Proc. 18th Plastic Pipes Conf. PPXVIII. (2016).