History
The Capital Region District comprises 13 municipalities that sought a new tertiary wastewater treatment plant that would help protect and maintain local waterways. The Wastewater Treatment Project officially began in April 2015, with Harbour Resource Partners as the project lead. The project comprises several components, including a new wastewater treatment facility, outfall system, and residual treatment facility. The new outfall pipe, which would be responsible for discharging the tertiary-treated effluent, would need to support high-volume flow.
Problem
CRD Wastewater Treatment Project initially specified 1800 mm steel pipes for its new outfall pipe. While the pipe would form an integral part of the project, its size and positioning (buried as deep as 60 m over the 2 km distance to the ocean) posed numerous challenges. A buried pipe would carry high maintenance costs if damage is detected. Designers sought a long-lasting pipe that would not corrode in order to reduce maintenance frequency.
Compliance and other requirements also caused the design to shift first to 2000 mm and then to 2250 mm. Finding a suitable pipe material and design within a short time frame proved challenging. AGRU helped the project designers put together an effective solution.
Solution
XXL HDPE pipe has not achieved widespread usage in the North American market due to a general lack of awareness of the product category’s capability and availability. But that is starting to change. With each successful project, engineers and customers are beginning to see the merits of super-sized HDPE pipe as well as the full scope of benefits associated with plastic’s versatility.
HDPE was eventually selected as the material of choice, with AGRU XXL HDPE pipe selected to be used in the outfall structure of the facility. The pipe’s usage of PE-100 was cited as a primary benefit—providing increased flexibility, durability, and longevity over competing products of the same size category. These physical properties facilitated installation. HDPE also promised to reduce maintenance costs and downtime due to its chemical stability and resistance to corrosion. Because AGRU’s XXL HDPE pipe is extruded rather than spiral winded, CRD was able to meet EN 12201 and ISO 4427 standards.
The move to HDPE also predicated on the creation of specialized fittings such as the Diffuser Pipe Section and the flange coupling adapter that would connect the HDPE pipe to a steel pipe section. Both fittings met design requirements and enabled the project to move forward.
Progress
Approximately 2000 m of AGRU XXL HDPE pipe, 110 pipe joints, 5 fittings, and 2 custom-fabricated assembly pieces were transported to the site to support the sink and deployment methodology selected for the pipe installation. The pipe and supporting pieces were all transported by flatbed truck with braces, caps, and saddle-style dunnage for the deck provided by AGRU. By sourcing the pipe and all associated fitting components (including elongated stub ends, elbow, a wall spool, a pump spool, and diffuser pipes) from AGRU, the designer ensured interoperability to improve the outcome of the installation. All pipe components were fusion welded together by fusion technicians who also received training from AGRU experienced technicians.
This project demonstrates many positive qualities of plastic pipes, but most importantly highlights the material’s customizability to meet changing requirements. This project achieves two milestones for plastics: The use of the largest pressure pipe in North America and the largest solid wall extruded HDPE pressure pipe in North America to be butt fusion welded.
The reduced weight of HDPE pipe (as compared with concrete and steel pipes of the same size category) has already provided cost savings for the client. The pipe’s weight, flexibility, and weldability also contributed to reduced installation labor and time. The customer is also expected to capture cost-savings over the next 50 years, the lifetime of the project, from reduced maintenance requirements.
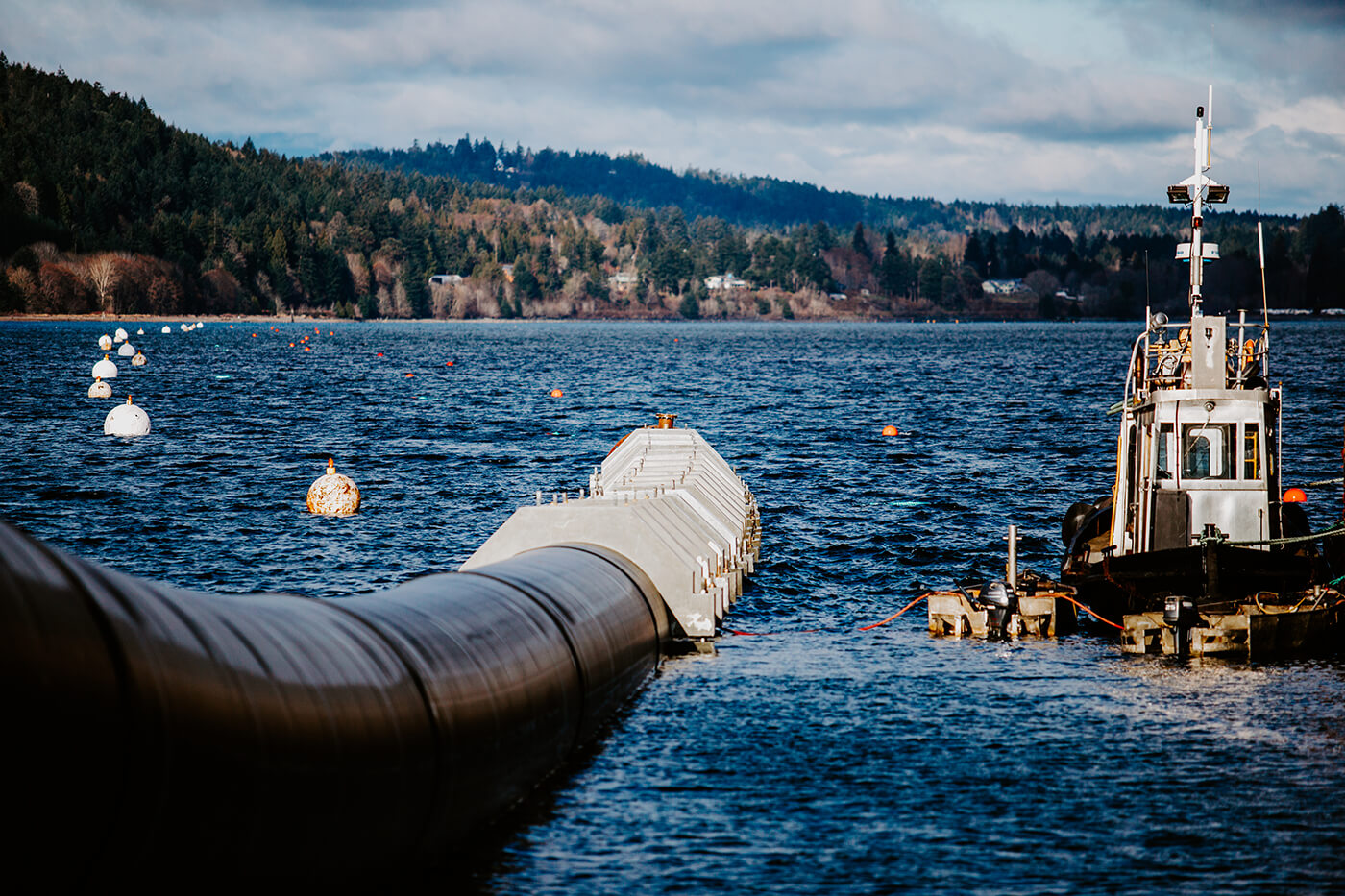
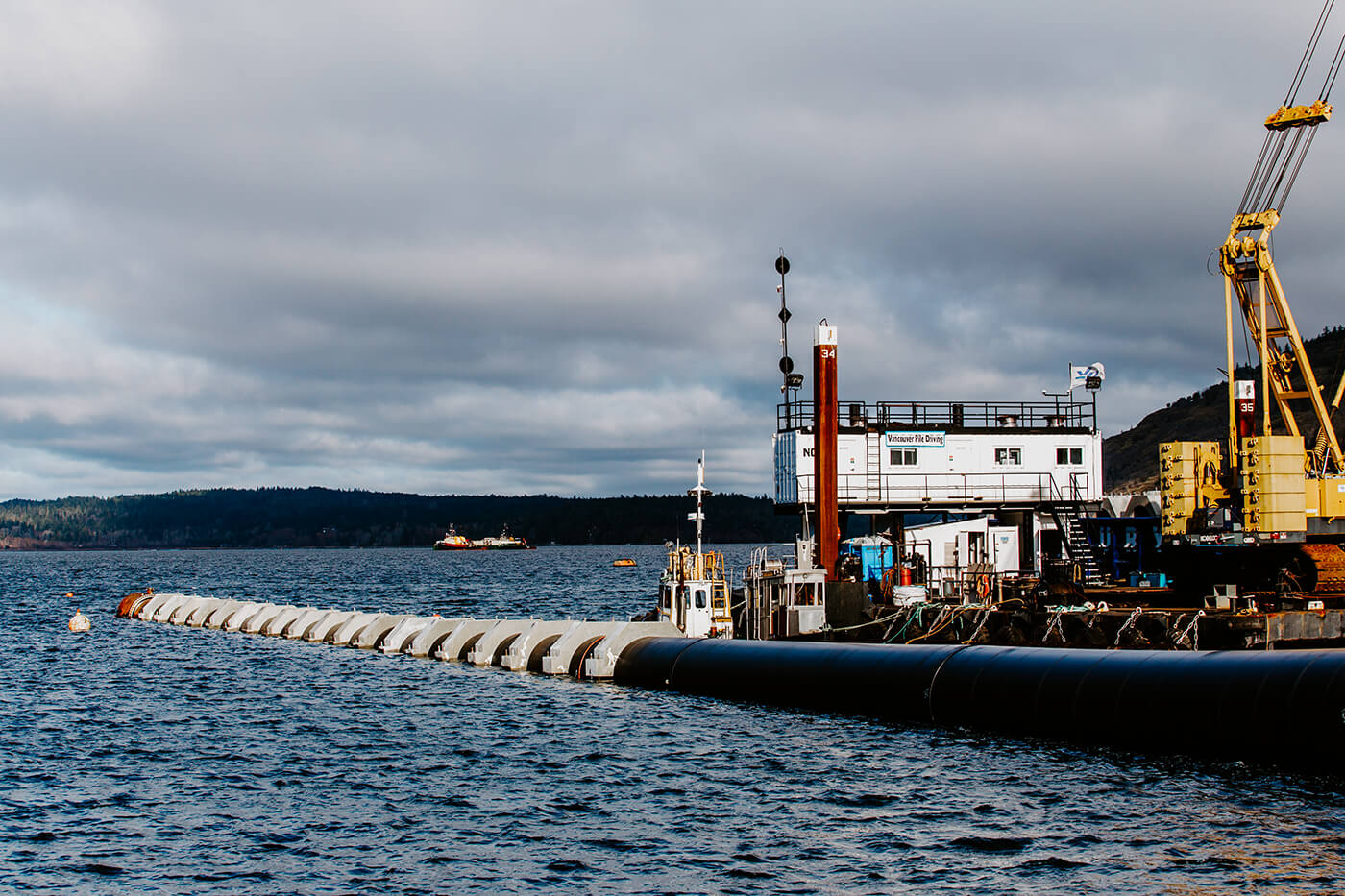
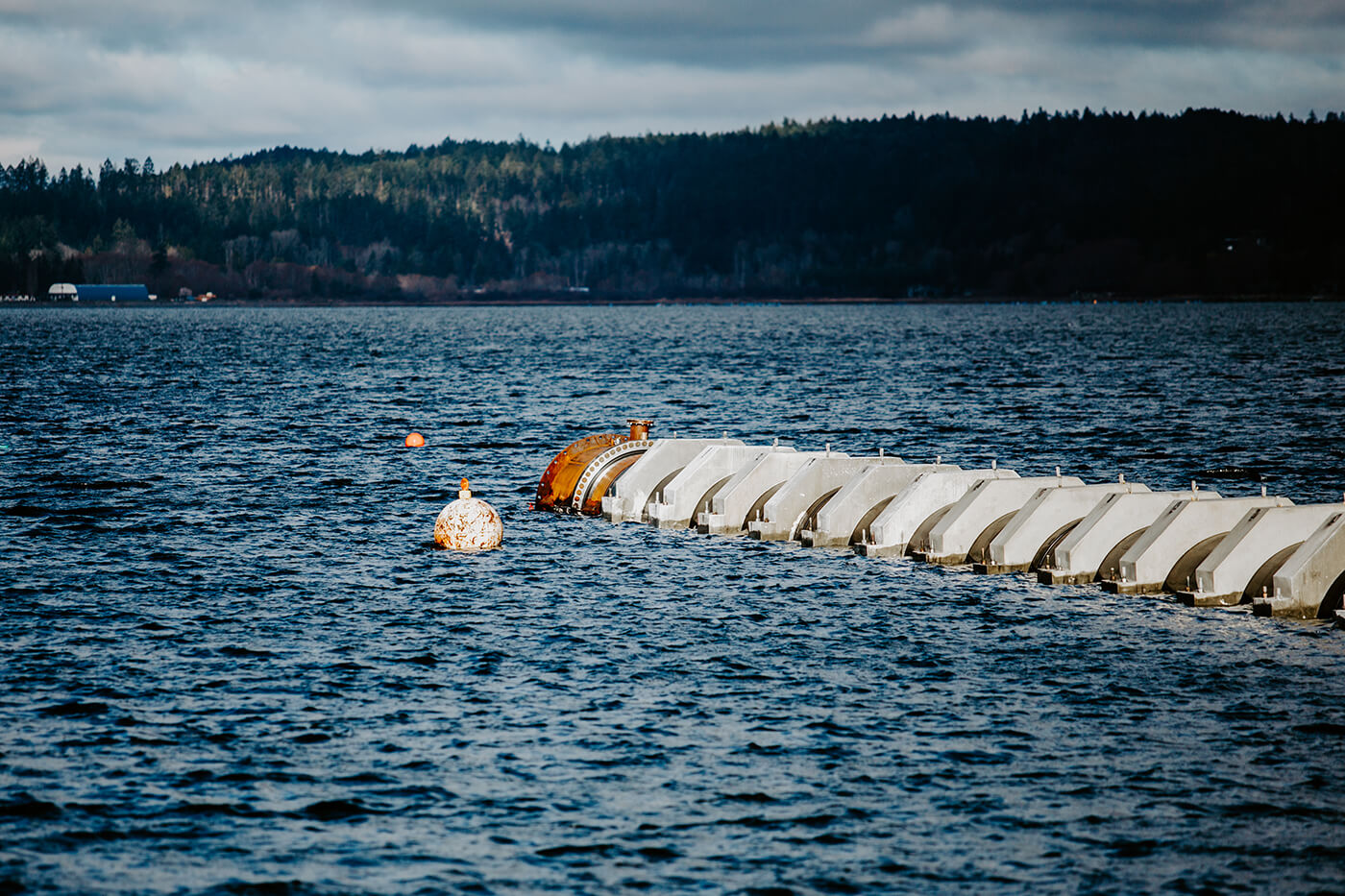
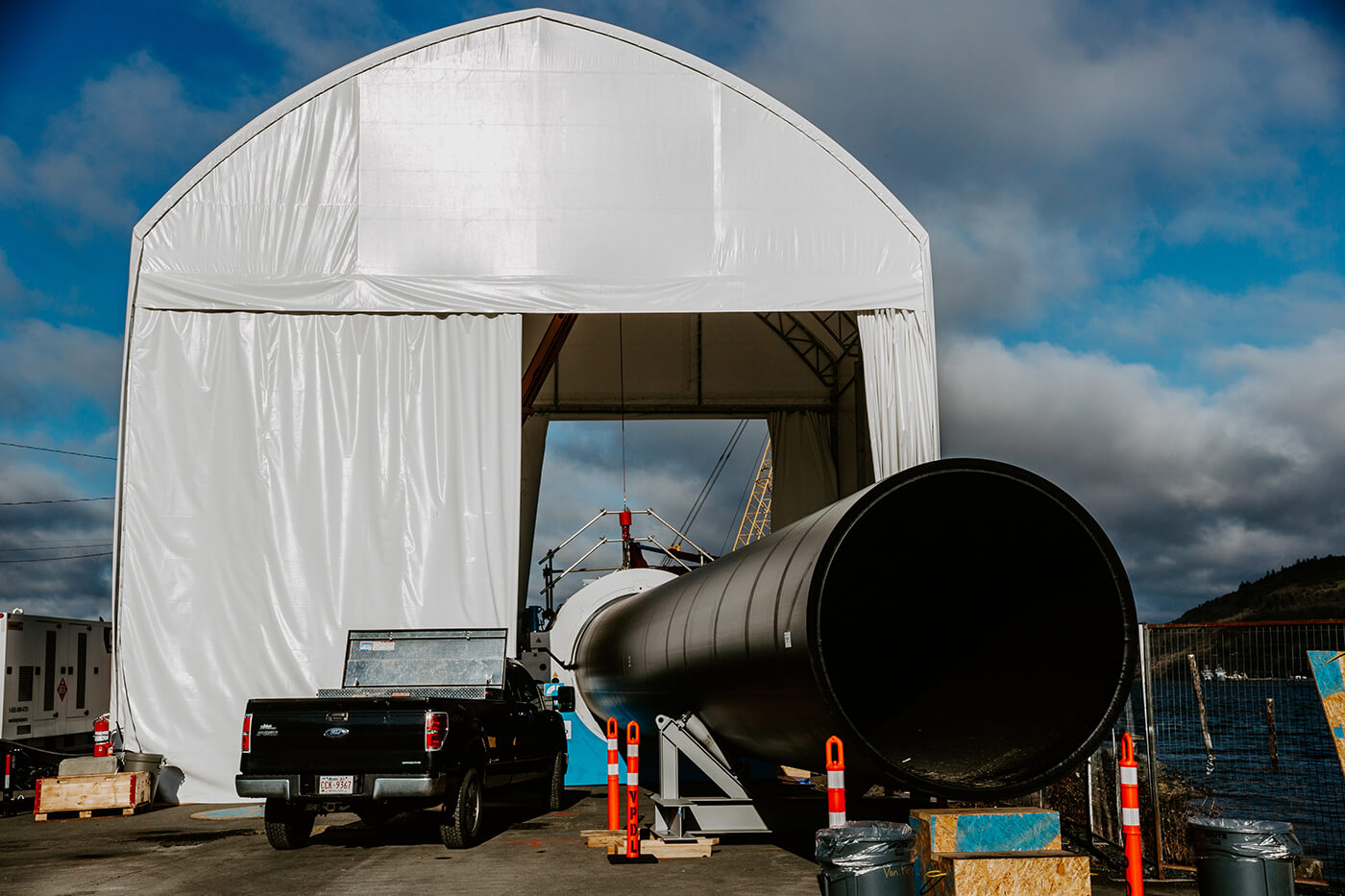
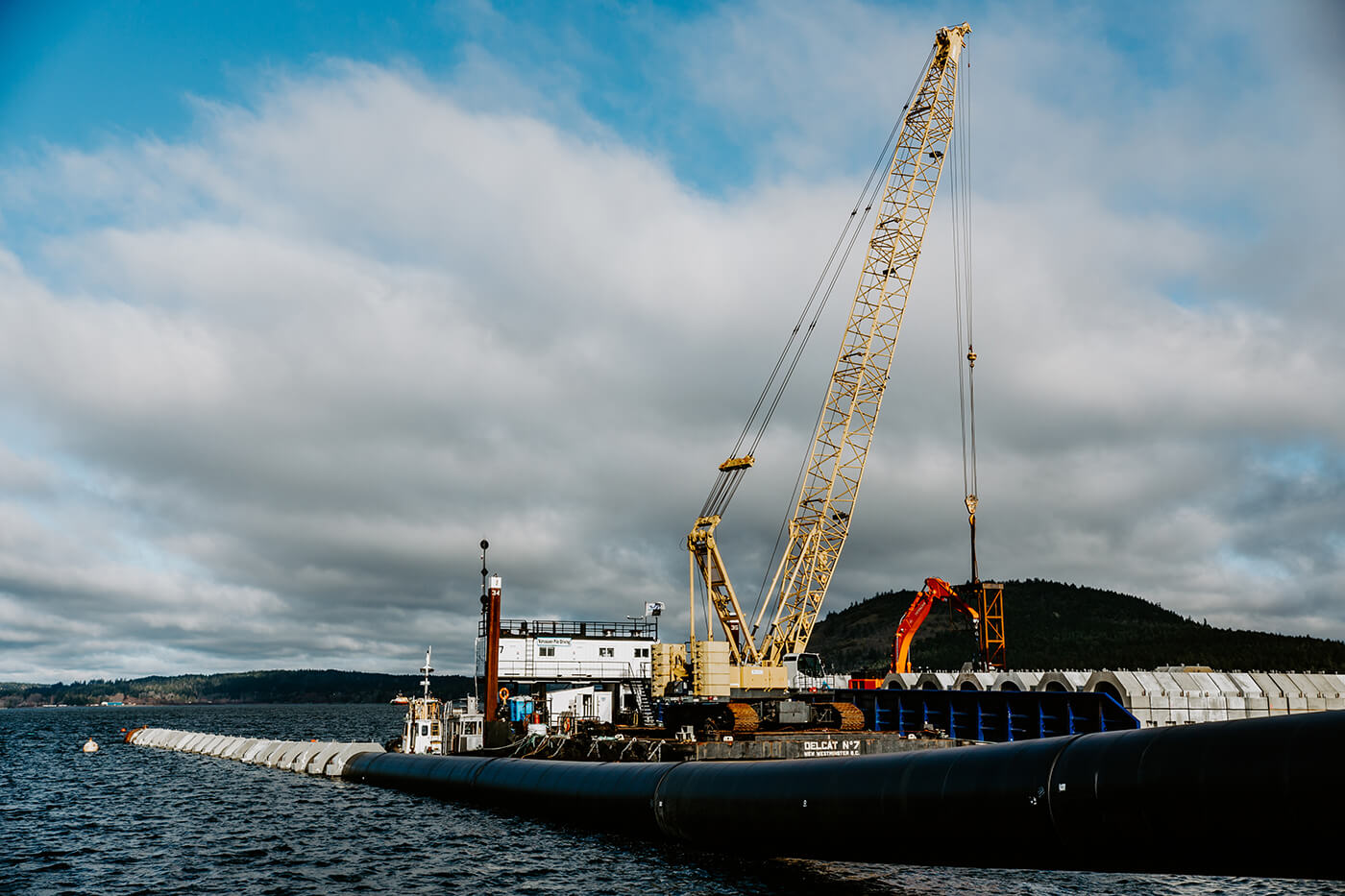
Overview
- Extruded High-Density Polyethylene Pipe
- Manufactured at OD 2250 mm
- SDR21(s = 107,2 mm) /SDR26 (s = 86 mm)
- PE100 resin
- Meet the EN12201/ISO 4427 requirements
Download Resources
Need Help Determining Which Product is Right For Your Application?
Interested in learning more about how one of our products can make a difference in your next project? Please reach out to us with your questions and one of our sales or technical staff will be happy to assist you.
We can help you determine your exact product or application-related needs. And because our products meet, and often exceed, industry standards you can rest assured knowing that you are getting the best solutions in the business.