History
The Huntington, Indiana landfill opened in 1970.
In the 1990s, booming growth in the city led to the acquisition of another nearby property for a planned expansion of the facility to meet future waste disposal needs. Officials estimated the upgraded facility could have a lifespan of between 20 and 80 years, depending on a number of factors including recycling efforts and actual population growth. Unfortunately, the recycling plan did not come through and the landfill experienced a surge in accepted waste between 2009 and 2014. By 2016, officials initiated the closure of the landfill’s first cell.
Problem
Despite having acquired additional property to expand its landfill capacity, Subtitle “D” introduced new rules and landfill location restrictions. For the Huntington landfill, the new rules prohibited the expansion as it was in proximity to a wellhead protection area. The rules also likely inhibited the landfill expansion efforts in nearby counties.
The surge in accepted waste reduced the landfill’s service life. The city prepared a post-closure plan addressing final grades and the utilization of a Subtitle “D” composite cover. The plan had to incorporate the closure of 60–65 acres of landfill that would be capped.
Solution
The City of Huntington, Indiana selected Strand Associates, Inc. as the design engineer for the closure project. To meet Indiana Department of Environmental Management (IDEM) regulations, AGRU’s technical team recommended a geosynthetic closure solution that included Super Gripnet geomembrane. Super Gripnet provided the required hydraulic barrier and lateral drainage for the closure system. The Super Gripnet system was designed to be covered with a nonwoven geotextile to provide the required filtration. Geocomposite was incorporated beneath the Super Gripnet geomembrane to provide methane gas ventilation.
“AGRU’s Super Gripnet is a top-performing liner and is often selected for its transmissivity performance and proven barrier capabilities,” says Mike Gnau, AGRU Regional Manager.
Linear low-density polyethylene (LLDPE) was selected for its excellent tensile properties. “LLDPE is better equipped to withstand differential settlement, which is common for capping applications,” says Mike.
For closure applications, the Super Gripnet drainage studs are installed facing up and covered with a nonwoven geotextile to provide the required filtration. The drainage layer produced between the geotextile and IDS geomembrane provide transmissivity values that can exceed conventional geocomposite under typical capping conditions. In addition to the superior drainage properties, the friction spikes on the bottom side provide excellent interface shear strength against soil.
“Factors such as the steepness of the slope, interface shear strength at low normal loads, and the management of landfill gas beneath the liner all affect veneer stability,” says Mike. “Our job is to ensure that we produce a liner product that meets or exceeds interface shear strength specifications to help engineers design a cover system that can avoid veneer failures.”
As part of AGRU America’s quality control process, the Super Gripnet batch was tested at AGRU’s GAI/LAP certified lab for quality. Samples were also sent to a third-party lab and to the engineer for testing with on-site soils.
Outcome
By October 2019, Taylor Geosynthetics and Clean Air and Water Systems completed construction of the closure cap. The construction was completed on schedule and passed all construction quality control checks.
Taylor Geosynthetics was responsible for the first phase of the installation in 2018 when the project was initially designed as a partial closure. By early 2019, a decision was made to completely cap the landfill. The second phase of the installation was handled by Clean Air and Water Systems.
“AGRU has been present here in North America for over three decades. In that time, we’ve developed domain expertise in delivering geosynthetics of the highest quality to help provide a host of solutions for municipalities,” says Rick Cannon, Senior Vice President at AGRU America, Inc. “Our portfolio of industry-leading products receives ongoing R&D from AGRU, our parent company in Austria and we are constantly adapting our operations to meet the challenges of the future.”
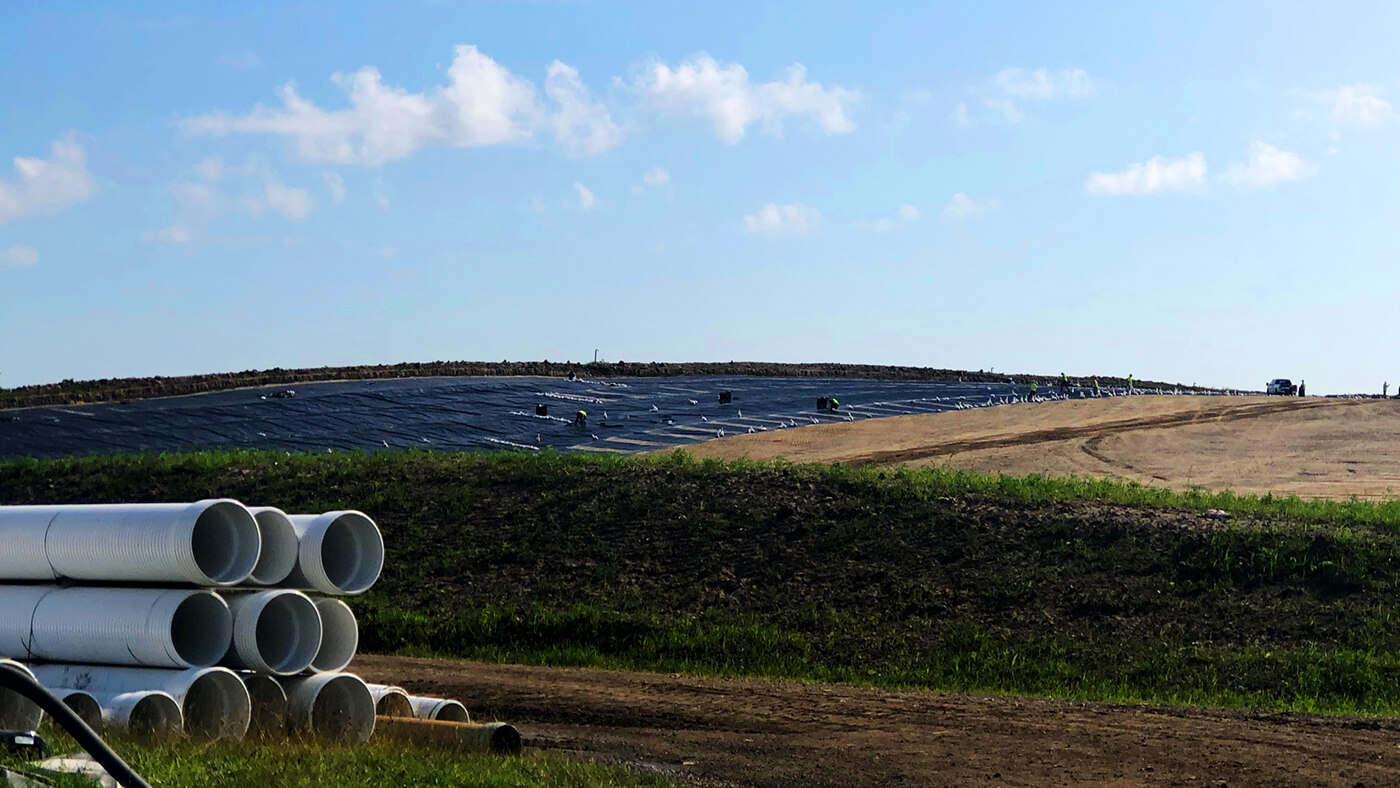
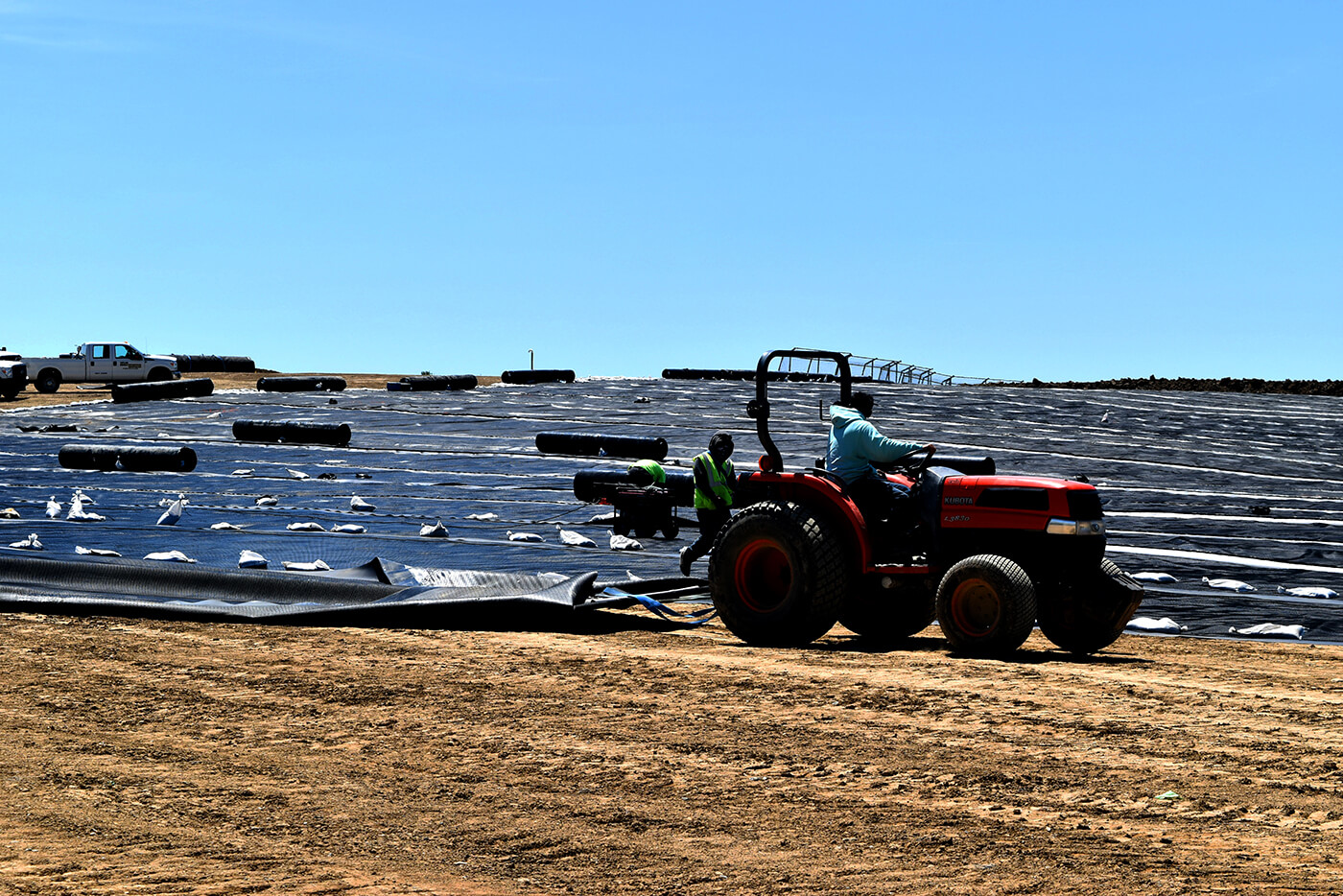
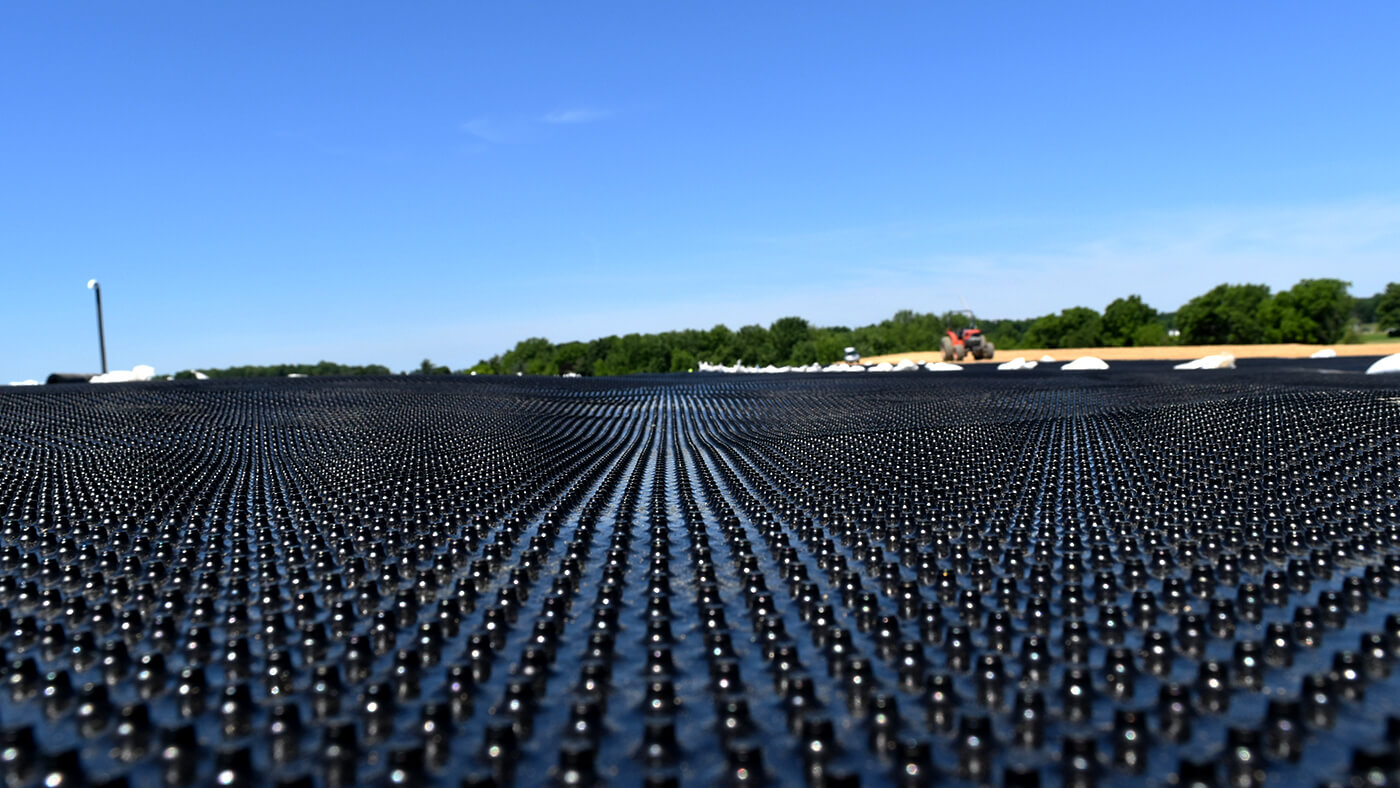
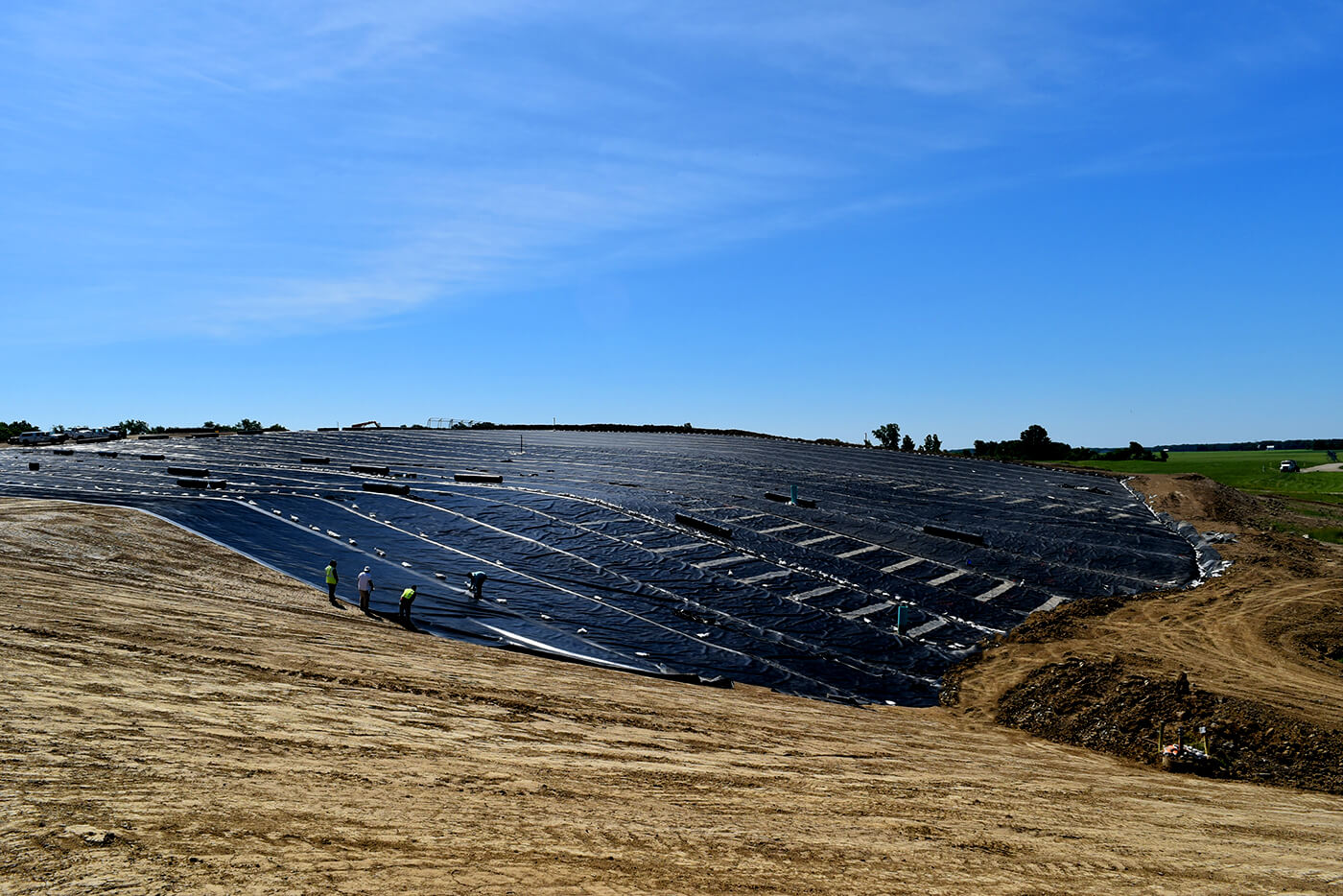
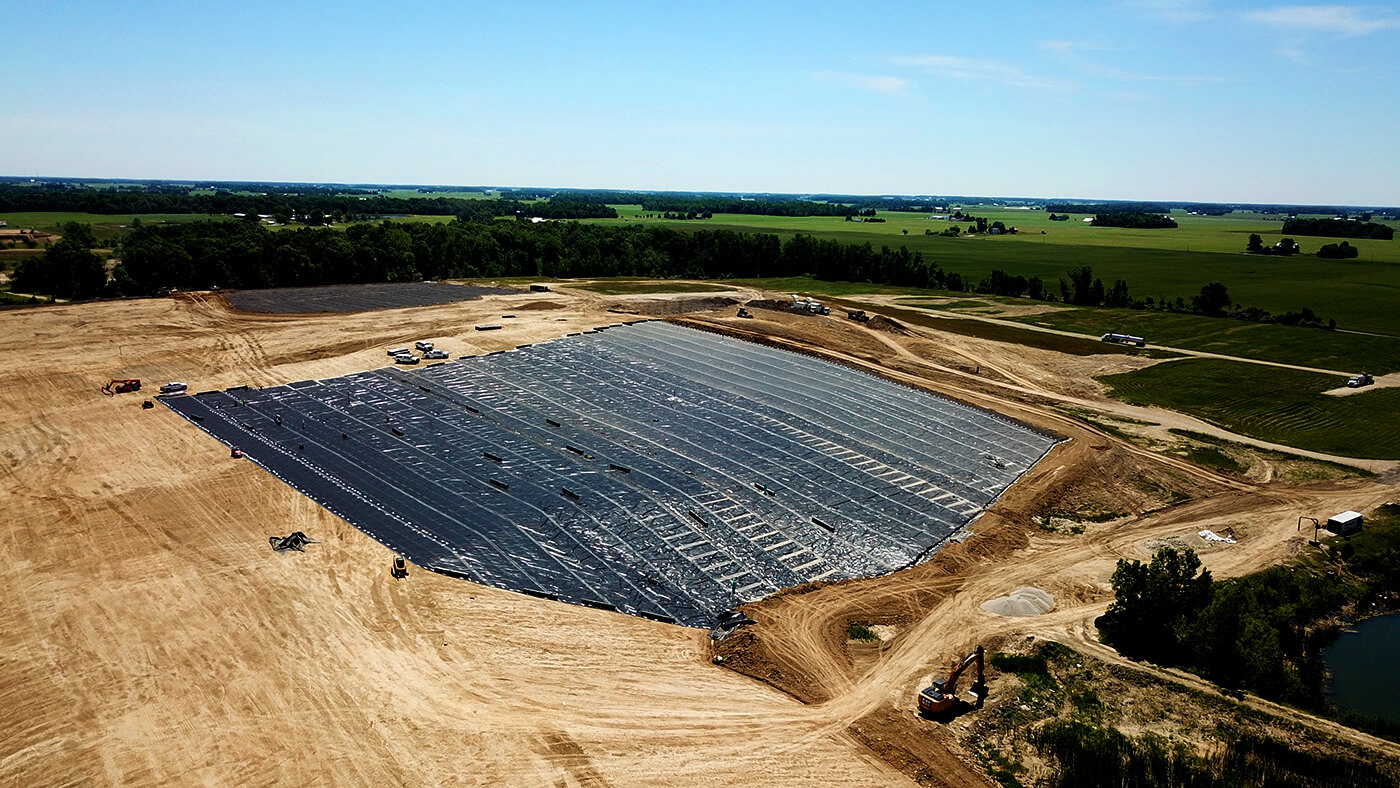
Overview
- Huntington, Indiana
- AGRU LLDPE Super Gripnet® 50 mil
- 6 oz. Double-Sided 250 mil Geocomposite
- AGRUTex® Nonwoven Needle-Punched Geotextile
Download Resources
Need Help Determining Which Product is Right For Your Application?
Interested in learning more about how one of our products can make a difference in your next project? Please reach out to us with your questions and one of our sales or technical staff will be happy to assist you.
We can help you determine your exact product or application-related needs. And because our products meet, and often exceed, industry standards you can rest assured knowing that you are getting the best solutions in the business.