Geomembrane and HDPE Welding is regarded both as an art and a science. While there are ways to predict a geomembrane’s performance under a variety of conditions, the sheer number of factors raises the level of complexity to the point where no prediction can come close to on-site testing. This article provides an overview of how to best perform geomembrane / HDPE welding in the field, including a summary of field welding under various conditions, field testing of seam integrity, and an introduction to new products that can enhance welding efficiencies.
Field welding best practices
The four most common ways of creating field seams for geomembranes are: hot wedge, hot air, ultrasonic, and extrusion fillet seaming (1). A preferred approach is to create dual bond tracks separated by a nonbonded gap, which is called a dual-track seam or double-track seam. The nonbonded gap can be used to evaluate seam quality and the continuity of the seam (air channel test) by pressurizing the space with air and monitoring for drops in pressure that signal a leak (2).
After choosing a weld method, geomembrane properties such as its type (e.g., high-density polyethylene), melt index, and thickness should be considered. These properties will affect the weld settings. For example, a higher melt index allows the seaming process to take place at lower temperatures and at higher speeds. Prior to any welding, the specific seam area should be cleared from all soil particles and other foreign matter (1, 4). Finally, before working on any production seams, trial seams should be conducted according to the construction quality assurance (CQA) plan (e.g., two trial seams a day, 3).
When using the hot wedge or extrusion fillet seaming approaches in cold weather (32° to 5°F), additional considerations are recommended. GRI GM9 offers a standard practice for cold weather seaming of geomembranes. Preparations include ensuring clear weather prior to seaming (do not field weld during snow, sleet, or hail) and removing all frost and moisture from seaming locations (3). Preheating the geomembrane area is also an option. If not preheated, field welding geomembrane in cold weather is usually slower than when welding at temperatures above 32°F. GM9 also recommends performing more frequent trial seams. To help deal with adverse weather conditions, tents or other moveable enclosures are sometimes used to facilitate field welding geomembranes.
Most CQA plans include details on field testing seam integrity. The next section will cover several approaches.
Field testing seam integrity
Modern recommendations for field testing seam integrity recognizes that different approaches can be taken based on welding practices. For example, utilizing certified installers, automatic welders, and other practices should mean less restrictive destructive seam testing intervals. If the standard destructive seam test interval for geomembranes is one sample per 500 ft, then the interval for a site that uses value-added practices could be one sample per 750 ft. Furthermore, using geomembranes that support testing using an electric leak location (ELL) method (ASTM D7240-18) should require even fewer destructive tests. Figure 1 outlines three different field-testing tracks based on welding practices. Please note, site-specific regulations can require a particular strategy and leave no room for options or changes (2).
Figure 1. Flow chart representing three different ways to test the field integrity of geomembrane seams, from reference 1.
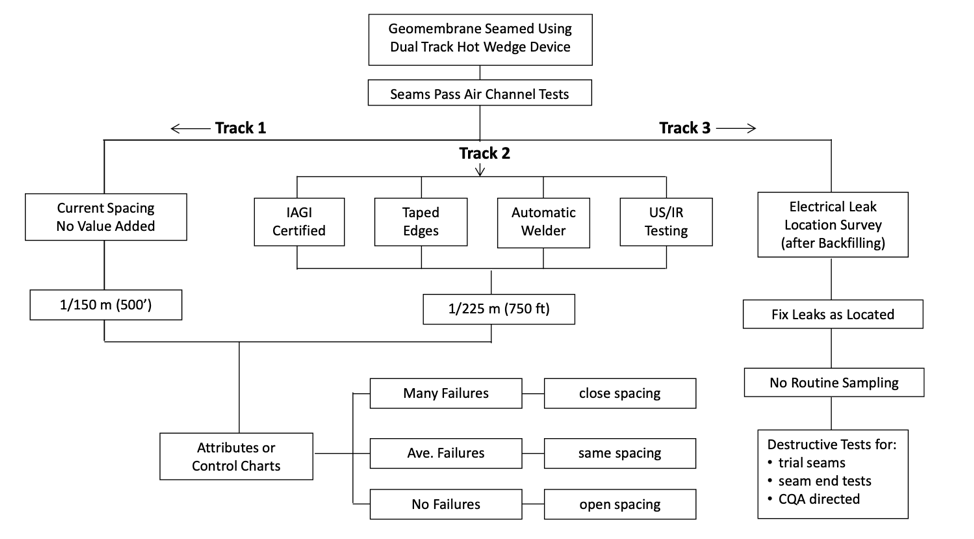
The destructive test method for typical geomembranes (HDPE, LLDPE, etc.) should follow ASTM D6392-12. GRI-GM19a provides additional reference data to help determine pass/fail conditions for seams based on shear strength, shear elongation, peel strength, and separation values in relation to geomembrane thickness (1).
Products that support modern welding practices
Modern welding practices not only improve welding efficiency, but can also reduce destructive testing requirements. New products can also support these welding practices; taped geomembrane edges are an example of such a product innovation. Taped geomembrane edges, like AGRU America’s CleanSeam™ technology, help safeguard the sheet by assuring dryness and cleanliness in the area to be welded (2, 5). CleanSeam is available with all AGRU geomembranes including Conductive Liner, which supports ELL testing. By incorporating taped geomembrane edges, conductive liner to support ELL, and other value-added practices, welders can help streamline their installation and field testing.
Engineers can also support their welders by choosing a geomembrane that facilitates the seaming process in the field. AGRU geomembranes are precision manufactured to the highest standards, demonstrating a consistent thickness throughout the liner as well as a high melt index. By choosing AGRU, engineers gain access to a competitive field welding solution that reinforces best practices.
Interested in learning more about field welding geomembranes or how AGRU solutions can support your next project? Reach out to an AGRU America representative using the link below:
Contact
References
- 1. “Standard Specification: Seam Strength and Related Properties of Thermally Bonded Homogeneous Polyolefin Geomembranes/Barriers.” Geosynthetics Institute. (2017). Accessed online 7 July 2020 at https://geosynthetic-institute.org/grispecs/gm19a.pdf.
- 2. “Standard Practice: Field Integrity Evaluation of Geomembrane Seams (and Sheet) Using Destructive and/or Nondestructive Testing.” Geosynthetics Institute. (2013). Accessed online 7 July 2020 at https://geosynthetic-institute.org/grispecs/gm29.pdf.
- 3. “Standard Practice: Cold Weather Seaming of Geomembranes.” Geosynthetics Institute. (2013). Accessed online 7 July 2020 at https://geosynthetic-institute.org/grispecs/gm9.pdf.
- 4. “How to Weld Geomembranes.” AGRU America. Accessed online 7 July 2020 at https://agruamerica.com/how-to-weld-geomembranes/.
- 5. Kelsey, “AGRU CleanSeam Protects Geomembrane Weld Edges in the Field.” Geosynthetica. (2020). Accessed online at https://www.geosynthetica.com/cleanseam-protects-geomembrane-weld-edges/.