For decades, steel has been used across all major parts of water supply systems, including in-plant piping systems, water storage, transmission and distribution mains, service lines, and residential and commercial buildings (1). However, our understanding of corrosion and its effects on system performance has revealed some drawbacks to the ubiquity of steel and other materials susceptible to corrosion. Specifically, the ability for corrosion to trigger failure in large-diameter pipes prone to corrosion. In fact, one case study has shown that large corrosion patches, rather than small pits, are the primary cause for failure. Implementing measures to prevent corrosion or using materials that resist corrosion is essential for creating last-lasting and efficient water supply systems (2).
The only other material that has been used as extensively as steel in water supply systems is polyethylene (1). In this article, we will compare the performance of steel with PE 100 and discuss how its chemical and physical properties make it a viable alternative to steel.
How does Steel and PE 100 materials perform in a water supply network
While both steel and polyethylene (PE) 100 materials can be used across all components in a water supply network, they aren’t equal in performance. For starters, steel can be used in thermal applications with temperatures exceeding 60°C, making them suitable for containing high temperature geothermal fluids. While PE 100 can’t be used at high temperatures, the material has been shown to be an effective steels substitute for low temperature geothermal fluids. In fact, one cost-benefit analysis showed that PE 100 outperforms steel both in performance and costs across many applications.
First, pipes and fittings made with PE 100 have lower costs across their service life because the material does not corrode, rust, rot, pit, tuberculate, or support biological growth. Because the material is resistant to corrosion, it does not need to be replaced or maintained in the same manner as steel. Additionally, PE 100 has a lower pumping cost throughout its service life. Using the water flow equation, where V water velocity, k is the conversion factor, C is the roughness coefficient, R is the hydraulic, and S is the slope of the energy line, it becomes clear that C is one of the most significant variables when determining water flow—all other factors being equal.
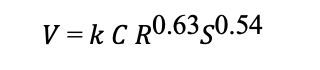
The roughness coefficient, C, refers to the smoothness of the inner surface of a pipe. New pipes typically start with a very high C coefficient, but that number decreases with time as the pipe deteriorates with age. There are several processes that can cause this, but the most typical one is tuberculation. Pipes will tuberculate as pitting corrosion products buildup. With time, the flow will become affected and can even be completely stopped. While steel can be affected by tuberculation, with its C coefficient decreasing by more than half in about 50 years, PE 100 pipes are unaffected (3).
Beyond corrosion, pipes and fittings made with PE 100 offer high resistance to seismic activity and are very easy to install thanks to its flexibility. Furthermore, PE 100 is one of the few materials able to be fusion welded to create leak-free joints. A leak-free pipe can help address problems typically associated with water supply systems such as infiltration and exfiltration. Due to its robustness and excellent service history, industries with mission-critical need for sustained water supply have become early adopters of PE 100. For example, a number of nuclear power plants in the United States have been using PE 100 instead of steel for safety-related piping systems. Steel pipes in these applications have been associated with high costs due to the operational cost of shutting down the plant during repairs. To save millions every year in repairs, power plants have transitioned to PE 100 as an alternative to steel pipes. PE 100 is also used within the Essential Service Water systems of nuclear power plants.
Where can you source PE 100 for piping systems in the United States?
PE 100 is used by AGRU America to manufacture high-density polyethylene (HDPE) pipes, pipe fittings, and valves. These products are made with the newest generation of Plastic Pipe Institute (PPI) and National Science Foundation (NSF) recommended materials and are part of its AGRULINE product line. AGRULINE meet a host of standards including ASTM D3261, ASTM D2513, NSF 61, and AWWA C901 and C906. AGRU has taken its pipe manufacturing a step further by incorporating a higher tier resin in its products, designated PE 100-RC. The RC in this case, signifies stress crack resistance. Products made with PE 100-RC are even easier and cheaper to install, and offer a higher safety factor in regions with expected seismic activity.
AGRU differentiates itself as a plastics manufacturer through flexible, solution-oriented service. AGRU’s approach allows the company to be a one-stop shopping point for all piping needs. For example, AGRULINE components are designed for interoperability and are precisely stocked to ensure reliable on-time delivery. AGRU also offers technical support as well as additional training for fusion welding.
Interested in learning more about using polyethylene in your next piping project? Reach out to an AGRU representative to learn more about AGRULINE.
Reach Out
References
- 1. “Corrosion Manual for Internal Corrosion of Water Distribution Systems.” (1984).
- 2. Kodikara et al., “Lessons Learned from Large-Diameter Pipe Failure Case Studies.” Pipelines. (2017).
- 3. Maingi, “High-Density Polyethylene (HDPE) as a Replacement Material for Carbon Steel Pipes in Geothermal Projects.” KenGen. (2017). http://pubs.geothermal-library.org/lib/grc/1033763.pdf.