Sewer repair is a pressing matter for municipalities across the United States as aging sewer systems begin to fail. The structural integrity of sewer systems is vital to public health, environmental conservation, and the overarching sustainability of urban landscapes. The significance of a resilient and trustworthy sewer infrastructure is escalating, particularly in rapidly expanding and urbanizing societies. Regrettably, the current state of many sewer infrastructures leaves much to be desired due to decades-old, corroded pipelines that pose a significant risk.
The United States has 800,000 miles of public sewer lines and 500,000 miles of private sewer laterals (1). Many of these have been compromised due to several factors, including aging, exposure to harmful chemicals, and environmental influences (2). In a recent evaluation, the American Society of Civil Engineers (ASCE) assigned a grade of D+ to the wastewater infrastructure within the United States, implying that its condition is severely deficient (3). From 2012 through 2018, the break rates were raised to 27%. By some estimates, more than 1.7 trillion dollars would be needed in water main investments through 2050 (4, 5).
Accordingly, the growing demand for superior quantity and quality of underground municipal infrastructures has imposed an escalating burden on planning, installation, and maintenance tasks related to these services (6). The addition of redundant systems has become critical in ensuring continual operations despite infrastructure failures and required repairs.
When high-density polyethylene (HDPE) pipes are not an option, concrete protective liner (CPL) technology offers a way to meld the benefits of HDPE with the strengths of concrete pipes. This article discusses the need for sewer pipes repair, highlights the capability of concrete protective liners in improving concrete pipe performance, and explores CPL service history.
The need for sewer repairs
The urgency for sewer repairs and the imperative revitalization of sewer infrastructure is a pressing concern that countless cities worldwide are currently wrestling with. The gradual deterioration of this infrastructure represents a widespread and significant challenge, primarily arising from two core issues: corrosion and microbial-induced corrosion (MIC) (7). Corrosion is a naturally occurring process typically caused by the chemical interaction between the sewer pipes and the substances that flow through them (8). Over time, this process can significantly weaken the integrity of the pipes, reducing their overall lifespan and effectiveness (9).
MIC is particularly challenging for sewer systems because it is a biochemical phenomenon associated with bacteria typically present in sewer systems. These bacteria produce corrosive sulfuric acid and gradually damage concrete sewer pipes, causing them to become thin and brittle (10). The effect can lead to many problems, including frequent sewer overflows, persistent leaks, and catastrophic failures in the worst-case scenarios. These issues result in costly repairs and replacements and pose public health and environmental risks.
Given the scale of this problem, the need for more durable, efficient, and cost-effective materials for sewer infrastructure is a top priority. HDPE pipes have emerged as a viable, long-term solution, offering notable advantages, including resistance to corrosion and exceptional service life and durability (11).
However, HDPE pipes are only sometimes practical to implement. In these situations, it is possible to maximize the performance of traditional piping systems, such as concrete pipes. In this application, HDPE liners, or CPL, can help protect concrete structures against corrosion and MIC (12). This innovative technology aims to protect concrete pipes, potentially extending their lifespan and reducing the need for frequent repairs or replacements.
Concrete Protective Liner (CPL) Technology for Sewer Repair
CPL function by adding a protective barrier between the pipe’s contents and the concrete pipe. The liner can be installed in numerous ways but is typically installed during concrete precast. This allows precasters to integrate the liner into the inner surface of the concrete pipe. The lining protects against corrosive substances and MIC, extending the pipes’ lifespan and diminishing the need for constant repairs or replacements (13). Table 1 summarizes the significant benefits of CPLs.
The application of CPLs has a proven track record in preserving concrete structures by enhancing their durability and thus prolonging their service life. The predominant advantage of CPLs is their capability to revitalize and augment the durability properties of concrete, such as resistance to abrasion, chemical attacks, and water penetrations, all at a low cost (13–15).
Other merits of CPLs include enhancing the resistivity of concrete structures to corrosion (8, 16–18). Historically, CPLs have been utilized as internal protection layers in sewer pipes, waterproofing membranes in tunnels, protective coatings against acidic attacks in tanks, and pile encasements in buildings near the sea (19).
CPL in Action
The integration of CPL is typically incorporated during the construction phase of a new concrete sewer infrastructure project. Engineers and pre-casters work collaboratively to specify and add the CPL during the process. The CPL is firmly anchored into the concrete, ensuring a durable bond to withstand heavy loads and high internal pressures.
An example of such an integration is using the CPLs produced by AGRU, which have proven capabilities and performance. These systems, Figure 1, have been used to enhance the performance of the Leesburg Wastewater System in Leesburg, Florida, to serve around 37,300 residential and 2,000 commercial customers. One of its lift stations using AGRU CPL recently reached its 25-year service milestone.
Conclusion
This article has brought attention to the issue of sewer deterioration caused by corrosion and microbial-induced corrosion, underlining the significant threats to public health, environmental safety, and urban sustainability. CPL is presented as a promising solution to these challenges.
By providing a protective barrier against corrosive substances and MIC, CPLs can significantly enhance the durability and longevity of concrete sewer pipes, curbing the requirement for constant, costly repairs or replacements. Therefore, implementing CPL technology in sewer infrastructure represents a significant step toward a more sustainable, cost-effective, and resilient urban future.
As the demand for improved wastewater management continues to grow, CPLs will undeniably play a pivotal role in shaping our response to our aging sewer infrastructure.
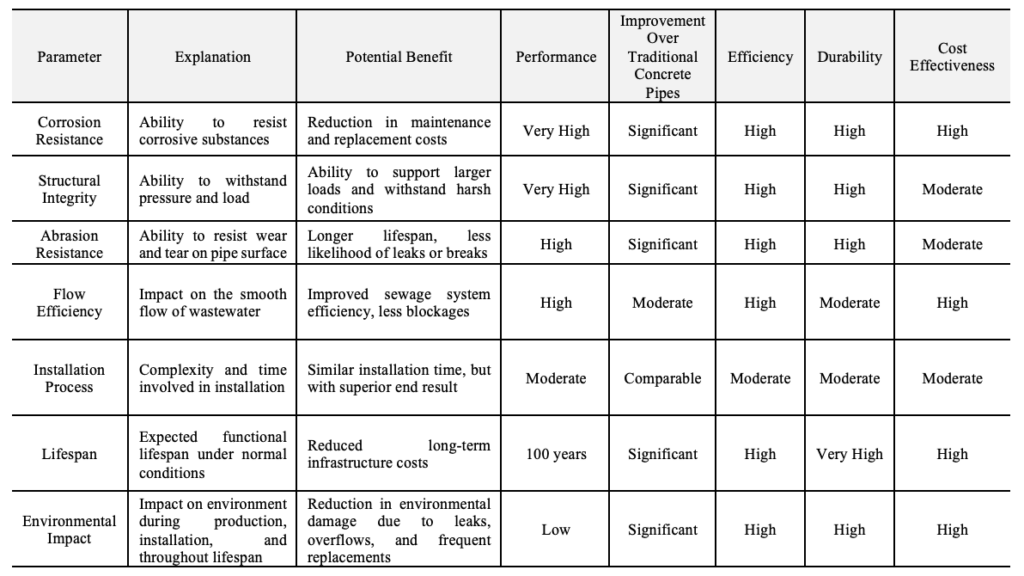
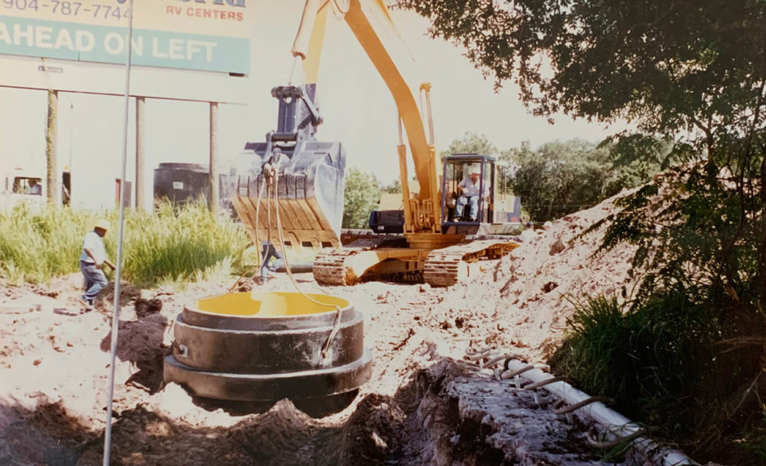
References:
1. R. Sterling et al. “State of technology for rehabilitation of wastewater collection systems.” U.S. Environmental Protection Agency. Washington DC. 2010.
2. M. M. Mohammadi et al. “Predicting condition of sanitary sewer pipes with gradient boosting tree.” in Pipelines 2020. 2020.
3. ASCE. “Infrastructure Report Card.” American Society of Civil Engineers. 2021.
4. S. Folkman. “Water main break rates in the USA and Canada: A comprehensive study.” 2018.
5. AWWA. “Buried No Longer: Confronting America’s Water Infrastructure Challenge.” American Water Works Association. 2011.
6. Y. J. Jung and S. K. Sinha. “Evaluation of trenchless technology methods for municipal infrastructure system.” Journal of Infrastructure Systems. 2007.
7. R. P. George et al. “Current understanding and future approaches for controlling microbially influenced concrete corrosion: a review.” Concrete research letters. 2012.
8. P. A. Schweitzer. “Corrosion-resistant linings and coatings.” CRC press. 2001.
9. N. Ghafari. “Investigation of water transmissivity of water-resistant concrete with acrylic polymer modifier used for improvement of tunnel temporary support.” 2011.
10. C. W. Fourie. “Acid resistance of sewer pipe concrete.” University of Cape Town. 2007.
11. K. Peterson. “HDPE pipe for corrosion-and leak-free operation.” ASHRAE Journal. 2017.
12. A. H. Nielsen et al. “Influence of pipe material and surfaces on sulfide related odor and corrosion in sewers.” Water research. 2008.
13. A. K. Parande et al. “Deterioration of reinforced concrete in sewer environments.” Proceedings of the Institution of Civil Engineers-Municipal Engineer. 2006.
14. B. Shojaei et al. “A review on the applications of polyurea in the construction industry.” Polymers for Advanced Technologies. 2021.
15. M. Sánchez et al. “External treatments for the preventive repair of existing constructions: A review.” Construction and Building Materials. 2018.
16. P. C. Hewlett. “Methods of protecting concrete—coatings and linings.” Protection of Concrete: Proceedings of the International Conference. 1990.
17. G. A. Whyatt and R. K. Farnsworth. “The high pH chemical and radiation compatibility of various liner materials.” Geosynthetic Testing for Waste Containment Applications. 1990.
18. C. Maraveas and A. A. Vrakas. “Design of concrete tunnel linings for fire safety.” Structural Engineering International. 2014.
19. P. G. Dimaio. “Introduction to Concrete Protection Liners.” Geo-Frontiers 2011: Advances in Geotechnical Engineering. 2011.
20. T. Abel and N. Pelczar. “Modern concrete pipes: a review of reinforcement and new technologies.” Studia Geotechnica et Mechanica. 2021.
21. N. Z. Muhammad et al. “Waterproof performance of concrete: A critical review on implemented approaches.” Construction and Building Materials. 2015.
22. M. Broekaert. “Polyurea Spray-Applied Systems for Concrete Protection.” In Fourth European Congress on Construction Chemicals. Nurnberg. Allemagne.. 2003.
23. D. Primeaux and J. Dudley. “Polyurea vs. polyurethane & polyurethane/polyurea: What’s the difference?.” In Proceedings of the Polyurea Linings Annual Conference. Polyurea Development Assocaition (PDA). Tampa. FL. USA. 2004.