Concrete and reinforced concrete pipes and containments are widely used for industrial applications such as wastewater plants, nuclear power, and geothermal power (1). However, these structures are vulnerable to chemical and biological interactions (2). Concrete protective liners are effective when used with concrete structures of high strength and stiffness, providing a barrier layer against these interactions by providing corrosion and abrasion resistance, flexibility, and ductility.
The central concept herein is to prevent the interaction between the concrete surface and contained liquid media to improve the longevity of structures used in industrial processes. This article discusses industrial applications of concrete protective liners, emphasizing their efficiency and capabilities.
Industrial Concrete Protective Liner Applications: Wastewater Treatment Plants
Modern wastewater management systems include sewers, chambers, pumping stations, maintenance holes, treatment facilities, and other components. It is estimated that there are 3 million kilometers of sewers and 18,000 wastewater treatment facilities in the wastewater management system of the European Union and over 16,000 in the United States (3). These structures are typically constructed of reinforced concrete (4). Indeed, sewage concrete structures are exposed to a corrosive environment below and above wastewater level. This environment induces concrete deterioration, representing a critical issue for stakeholders and decision-makers in wastewater collection and treatment facilities (5).
A study on this issue has reported the existence of severe deterioration with a maximum depth exceeding 2 cm in concrete pretreatment tanks after just two years of service (4). In addition to the physical and chemical impacts, microbial attacks are recognized as a primary source that induces concrete degradation. This is because the metabolic activity of many bacteria produces acids that contribute to concrete deterioration (6). A summary of microbiologically induced corrosion is shown in Figure 1.
Concrete tanks and other structures in wastewater treatment facilities are often protected against corrosion by applying a coating or lining material such as polyester, bitumen, epoxy, polyvinyl chloride, or polyurethane-based agents (7). These materials help to create a low-permeable, acid-resistant physical barrier between the concrete and a corrosive environment. On the other hand, coating failures in wastewater treatment facilities have been observed across the United States (8, 9). Besides, a study has described six coatings cases where blistering failed after 10 to 14 months of service in wastewater treatment plants (10). Failures such as this, when left unchecked, can result in severe structural deterioration and a significant reduction in the system’s life expectancy, as well as system interruptions and environmental impacts.
Furthermore, the inconvenience of service interruptions requiring bypass systems can add to the cost of the repairs and reapplications of coatings that will eventually be needed. In contrast, studies have reported the superiority of concrete protective liners (such as polyethylene) for long-term improvement of the resistance of concrete structures in direct contact with aggressive media at wastewater plants (11, 12). As a result, concrete protective liners are used to improve the durability of modern sewer structures (13).
Industrial Concrete Protective Liner Applications: Nuclear Power Plants
Typically, concrete containments in power plants are equipped with steel liners to provide leak tightness. These steel layers are often painted or lined to achieve corrosion resistance and decontamination. Moreover, part of the liner near the containment bottom and above the basement is often immersed in concrete to protect it from corrosive liquids. Indeed, corrosion is the primary degradation factor for the liner plate and structural steel (15). A study regarding this issue has reported the corrosion of steel liners’ outer and inner diameters for various reasons, including the presence of water or ice inside the containment and foreign materials in contact with steel (16).
The severity of this issue when it comes to nuclear power plants is represented by the impact of these local attacks on the leak potential of hazardous materials. As a result, the liner plate and any installed steel components can be lined with an appropriate membrane liner to resist the attack of the media (17). Furthermore, various lining materials, including concrete protective linings and fabric-backed applied membrane liners, are also used to protect the water systems at nuclear power plants (18).
Industrial Concrete Protective Liner Applications: Geothermal Power Plants
In geothermal power facilities with condensed steam cooling systems, microbial activity represents a critical operational concern. This steam may contain contaminants such as hydrogen sulfide, ammonia, carbon dioxide, and entrained liquids with dissolved solids (18). Most of these gases are removed from the condenser; however, some are dissolved into the cooling liquid (19). These dissolved gases, along with the dissolved solids, provide a nutrient source for the cooling water system’s bacteria.
Moreover, corrosion’s chemical treatments, cooling water cycles, and changes in thermodynamic or chemical conditions increase the potential for biofilm development. These operations result in high risks for microbiological attacks or microbiologically influenced corrosion that deteriorates concrete cooling tower basins in geothermal power plants(20). Such attacks are typically caused by sulfur-oxidizing bacteria such as Thiobacillus, which produces a corrosive agent known as sulfuric acid (H2SO4) that is significantly aggressive to concrete (5).
The interaction between the sulfuric acid and the cement matrix involves an acidic reaction with the calcium hydroxide (Ca(OH)2) that forms calcium sulfate (CaSO4) as follows:
Ca(OH)2 + H2SO4 → CaSO4 + 2H2O
The calcium sulfate is further hydrated to form gypsum (CaSO4∙2H2O). At this stage, a soft white substance forms on the concrete surface (21). In the event of a continuing attack, the gypsum reacts with the calcium aluminate hydrate (C3A) to form an expansive product called ettringite ((CaO)3∙(Al2O3)∙(CaSO4)3∙32H2O) as follows (22):
3CaSO4∙2H2O + 3CaO∙Al2O3 + 26 H2O → (CaO)3∙(Al2O3)∙(CaSO4)3∙32H2O
Once the ettringite is formed, the concrete structure undergoes extensive damage from the outer surface to the inner core due to the expansions (23). As a result, the concrete structure’s operation life is considerably reduced. To mitigate this issue, engineers and designers tend to utilize coating materials or concrete protective liners to prevent direct interaction between the concrete surface and the liquids’ biofilm (24–26).
On the other hand, bacteria such as Thiobacillus produce acids that lower the pH of the liquid and thus dissolve conventional protective layers over time (27). A study regarding this topic has compared various concrete mixtures with cementitious materials such as silica fume and blast furnace slag, as well as different coating materials, including epoxy- and latex-modified mortars (20). The study results, Figure 2, showed that the uncoated concrete specimens with various cementitious materials and the coated ones had undergone different degrees of deterioration during the laboratory tests. Therefore, to overcome this issue and achieve exceptionally high resistance to aggressive media, it is essential to cover the concrete surface with a protective layer from materials of non-polar nature, such as polyethylene resins typically used in industrial concrete protective liner systems (28).
Conclusion
This article has explored various industrial concrete protective liner applications. It was shown that concrete structures are susceptible to microbial activities that induce corrosion damage. This issue can be overcome by adding a protective layer, preferably from a non-polar material such as a polyethylene concrete protective liner, to provide a barrier that prevents direct contact between aggressive media and the concrete surface. The applications of this technique are expected to increase the service life of industrial concrete containments and pipes due to the material’s exceptional corrosion resistance and high durability.
Figures
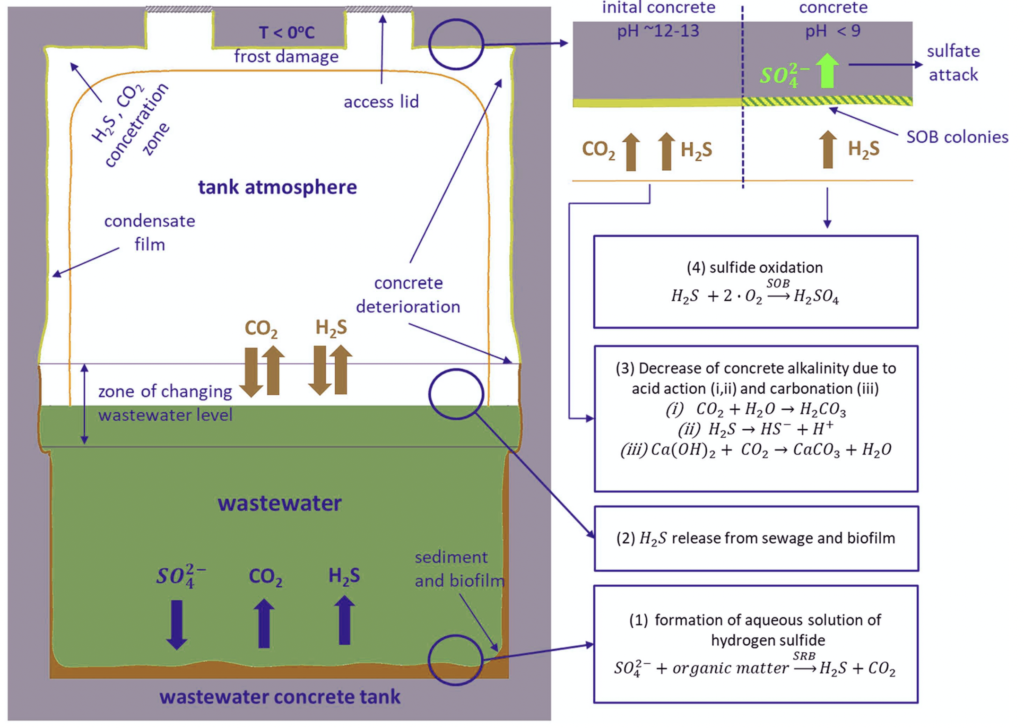
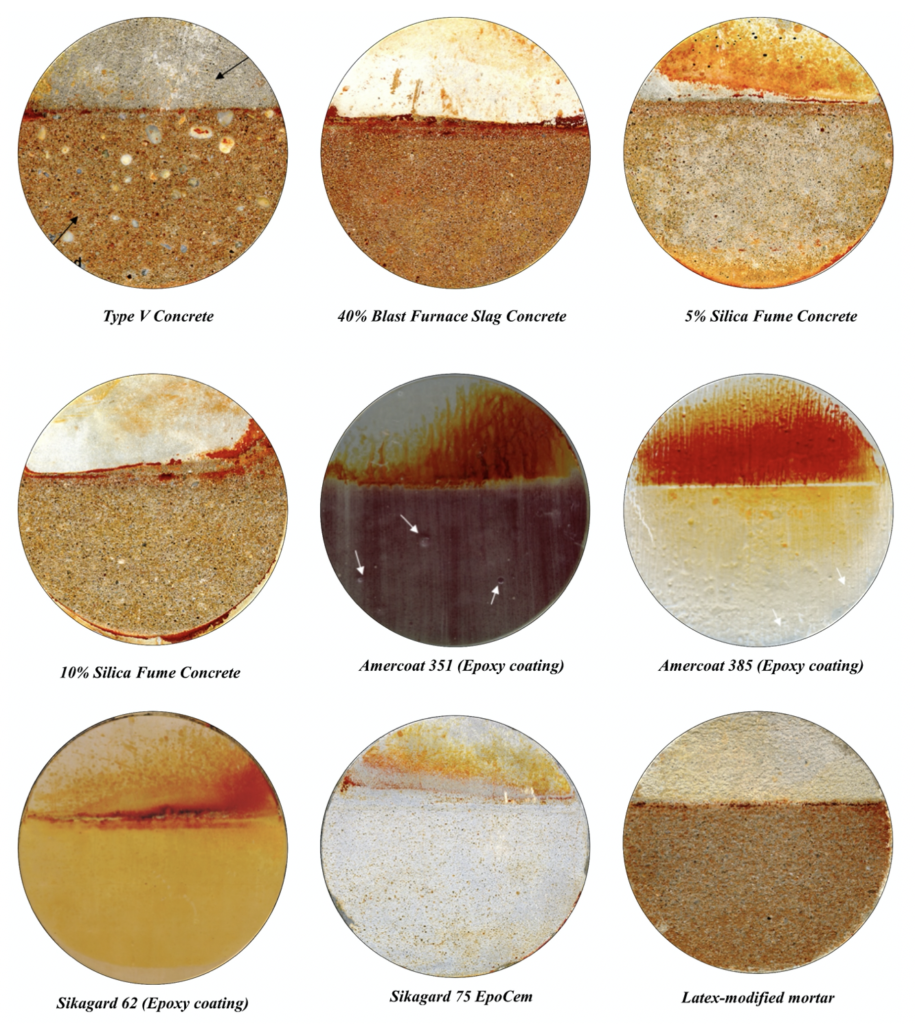
Interested in learning more about concrete protective liners in industrial applications? AGRU America manufactures industry-leading AGRU-ULTRA GRIP® for top-of-the-line concrete protection against corrosion and other aggressive media, with a patented anchor system for exceptional pull-out resistance.
Learn more
References
(1) B. P. Zlobenko. “Assessment of the Biodegradability of Containers for Low and Intermediate Level Nuclear Waste.” (2013).
(2) V. Kaushal et al. “Qualitative investigation of microbially induced corrosion of concrete in sanitary sewer pipe and manholes.” Pipelines 2018: Condition Assessment, Construction, and Rehabilitation. (2018). https://www.osti.gov/biblio/911257
(3) “Europe’s water in figures. An overview of the European drinking water and waste.” The European Federation of National Water Services. (2017).
(4) P. Woyciechowski. “Concrete corrosion in a wastewater treatment plant–A comprehensive case study.” Construction and Building Materials. (2021).
(5) M. O’Connell et al. “Biochemical attack on concrete in wastewater applications: A state of the art review.” Cement and Concrete Composites. (2010).
(6) L. Kong et al. “Assessment of coatings for protection of cement paste against microbial induced deterioration through image analysis.” Construction and Building Materials. (2018).
(7) T. Noeiaghaei et al. “Biogenic deterioration of concrete and its mitigation technologies.” Construction and Building Materials. (2017).
(8) G. Hall. “Out of sight, out of mind, and often out of order: The problems with protecting wastewater treatment plants.” Journal of protective coatings & linings. (2004).
(9) J. A. Redner et al. “Evaluation of protective coatings for concrete.” County Sanitation Districts of Los Angeles County, California. (2004).
(10) R. A. Nixon. “Coating Selection Guidelines for Changing Exposure.” JPCL. (2001).
(11) R. Nixon. “Linings in Wastewater Plants: Real World Performance Evaluation.” Journal of Protective Coatings & Linings. (2008).
(12) J. B. Soebbing et al. “Rehabilitating water and wastewater treatment plants.” Journal of Protective Coatings & Linings.
(13) P. G. Dimaio. “Introduction to Concrete Protection Liners.” In Geo-Frontiers 2011: Advances in Geotechnical Engineering. (2011).
(14) V. N. Shah and C. J. Hookham. “Long-term aging of light water reactor concrete containments.” Nuclear Engineering and Design. (1998).
(15) B. A. Erler et al. “Nuclear containment steel liner corrosion workshop: final summary and recommendation report (No. SAND2010-8718).” Sandia National Laboratories, California. (2011).
(16) D. J. Naus et al. “Report on aging of nuclear power plant reinforced concrete structures (No. NUREG/CR–6424).” Nuclear Regulatory Commission. (1996).
(17) G. V. Spires and K. T. PE. “Practices for Improving the Performance of Linings in Water Systems at Nuclear Power Plants.” Journal of Protective Coatings & Linings. (2001).
(18) E. T. Eliasson et al. “Geothermal power plants.” Short Course on Geothermal Drilling, Resource Development and Power Plants, Santa Tecla, El Salvador. (2011). Accessed online 16 August 2022. http://www.os.is/gogn/unu-gtp-sc/UNU-GTP-SC-18-12.pdf
(19) P. Pryfogle. “Monitoring biological activity at geothermal power plants (No. INL/EXT-05-00803).” Idaho National Lab. (2005). Accessed online 16 August 2022. https://www.sciencedirect.com/science/article/pii/0040609080905556
(20) M. L. Berndt. “Evaluation of coatings, mortars and mix design for protection of concrete against sulphur oxidising bacteria.” Construction and Building Materials. (2011). Accessed online 16 August 2022. https://doi.org/10.1016/j.conbuildmat.2011.04.014
(21) J. L. Davis et al. “Analysis of concrete from corroded sewer pipe.” International Biodeterioration & Biodegradation. (1998).
(22) R. P. George et al. “Current understanding and future approaches for controlling microbially influenced concrete corrosion: a review.” Concrete research letters. (2012).
(23) M. Basista and W. Weglewski. “Micromechanical modeling of sulphate corrosion in concrete: influence of ettringite forming reaction.” Theoretical and Applied Mechanics. (2008).
(24) T. Abel and N. Pelczar. “Modern concrete pipes: a review of reinforcement and new technologies.” Studia Geotechnica et Mechanica. (2021).
(25) L. Bacon et al. “Microbiology and corrosion in natural draft cooling towers.” Proceedings of the World Geothermal Congress, Florence, Italy. 1995.
(26) R. R. Reeber. “Coatings in geothermal energy production.” Thin Solid Films. (1980).
(27) R. Tewari et al. “Influence of microbes in cooling tower: a review.” International Research Journal of Engineering and Technology. (2019).
(28) D. R. Chapman. “Selection and design of corrosion protection liner for precast concrete segment tunnel liner.” in CRC Press. (2021).