Engineers must consider the durability and service life of all the required construction materials in a project. Data sheets and on-site testing results are referenced to ensure desired specifications are met. And while geosynthetics are often touted in the industry as durable and long-lasting materials, engineers typically require a more thorough analysis of a material before making a decision.
This article will summarize results from several reports regarding the durability and service life of high-density (HDPE) geomembranes. We will provide an overview of HDPE geomembrane, highlight typical mechanisms of degradation, and discuss ways HDPE liner manufacturers like AGRU help further improve the durability and service life of geomembranes.
An overview of HDPE geomembrane durability and testing
Geomembranes, or geosynthetic barriers, are planar sheets that are relatively impermeable to liquids. The sheets can be made with a variety of polymers including HDPE, linear low-density polyethylene (LLDPE), polyvinyl chloride (PVC), and polypropylene (PP). The physical and mechanical properties of polyethylene (PE) geomembranes (and classification) can differ significantly depending on the density of the resin. When the PE resin density is greater than 0.940 g/cm3, for instance, the PE is referred to as high density. In general, as the density increases, so does the geomembrane’s hardness, tensile strength, and chemical resistance (see Figure 1). Other factors that affect durability include geomembrane thickness, purity of the raw materials (and presence of impurities), degree of mixing and the processes used to create the geomembrane.
Figure 1. Generalized relationships between density of PE and material properties, from reference 1.
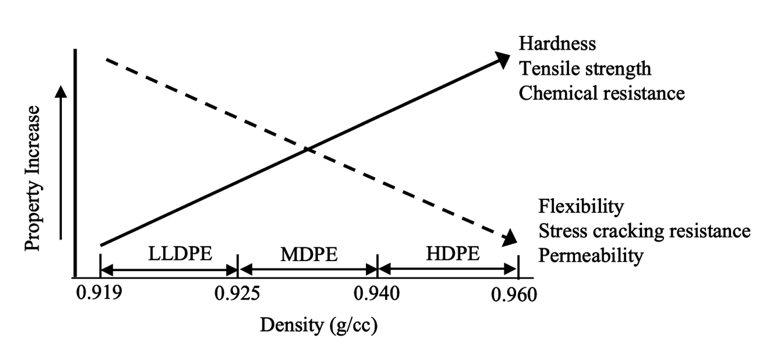
Geomembranes and most other geosynthetics have developed a reputation of durability as a result of many successful projects spanning over 50 years. Researchers have analyzed data from these past projects to develop a deeper understanding of the mechanisms behind the chemical degradation of geosynthetics. Studies have also led to the creation of screening and index tests to help predict performance of new geosynthetic products under differing conditions.
Tests (outside of design tests) fall under three different categories: direct measurements on exhumed materials, index tests, and accelerated tests. These tests can be used in different situations to estimate a product’s service life. Testing predicts projected service life based on how specific geomembranes react under conditions that eventually degrade the material.
Typical ways geomembranes degrade
Geomembranes and other geosynthetics will eventually degrade, but there are a number of factors that can cause them to start degrading early. Production failures, mechanical damage during transport, exposure to high temperatures for long durations, installation damage, and weathering are all factors that can damage geomembranes before they start to function. On the other hand, once they are installed there are factors that can accelerate degradation of geomembranes. Degradation factors include mechanical and dynamic loads causing creep and fatigue, seismic activity causing mechanical stresses, and slow chemical attack over time due to oxidation.
While geomembranes made with PE possess antioxidants, these chemicals are consumed over time. Therefore, excluding all other factors, the maximum service life of geomembranes is determined by the liner’s rate of oxidation. Oxidation refers to the loss of electrons and the rate of oxidation is determined by environmental factors such as temperature, oxygen partial pressure, and chemical composition of the surrounding media (1). Temperature has the largest effect on oxidation as it affects both oxygen solubility and permeability. Oxygen concentration is also an important factor as it is an essential element in most oxidation reactions for geomembranes. Finally, the presence of certain metallic ions such as cobalt manganese, copper, and iron in the media in contact with geomembranes can accelerate oxidation.
In essence, the durability of a geomembrane refers to not only the physical strength of the material, but also all the ways the product was created in order to reduce the rate of oxidation.
How HDPE liner manufacturers improve the durability and service life of geomembranes
Understanding the service life of a geomembrane is important because applications can differ in requirements, based on how the geomembrane will be used. Engineers must not only choose the right product for the right application, but also be confident that the selected product will perform according to specification (see Table 1).
Table 1. Typical design lifetimes, from reference 2.
Separator as construction aid | 0.5–1 year |
Separator (permanent) | 80–100 years |
Filter in drainage applications, replaceable | 10–25 years |
Filter in drainage applications, not replaceable | 80–100 years |
Reinforcement in a dam against slip failure | 5 years |
Reinforcement in retaining structures | 80–100 years |
Prefabricated vertical drain | 1–3 years |
Landfill liner, drainage, and protection | 100+ years |
Tunnel liner | 100+ years |
HDPE liner manufacturers like AGRU can directly improve the durability and service life of geomembranes through a number of manufacturing decisions. As mentioned before, the thickness of a geosynthetic product is an important factor that affects its durability (thicker geomembranes are slower to oxidize, 1). By incorporating a streamlined manufacturing process called flat-die extrusion and accurately regulating the temperature throughout the extrusion process, AGRU can produce a highly consistent liner with uniform thickness spanning the entire sheet.
The density and crystallinity of PE geomembranes can also affect how oxygen diffuses through the material. The denser HDPE geomembrane, for instance, has higher crystallinity and therefore reduces oxygen diffusion, reducing the material’s susceptibility to oxidation (1). By using quality HDPE resins, AGRU is able to manufacture a geomembrane that offers more resistant to oxidation. And by offering geomembranes infused with carbon black as an ultraviolet stabilizer, AGRU liners are better suited to a wider range of outdoor conditions.
Finally, AGRU manufactures specialized geomembranes that combine a variety of products into one solution capable of enhanced performance. A recent case study demonstrates how AGRU Integrated Drainage System (IDS) was used to decrease installation cost and improve closure system performance. The project engineers implemented an onsite test pad with the solution to verify the design decision, which ultimately allowed them to increase the maximum particle size specification by using IDS (3).
Interested in learning more about the durability and service life of geomembranes? Reach out to AGRU, an HDPE liner manufacturer with over 70 years in the business.
Speak to a Representative
References
- 1. G. Hsuan et al., “Long-term performance and lifetime prediction of geosynthetics.” EuroGeo4 Keynote Paper. (2008). Accessed online at https://pdfs.semanticscholar.org/5098/e4606b93a143ab69fd902ed3f50eac826bde.pdf.
- 2. H. Greenwood et al., “Durability of Geosynthetics.” CUR. (2012). Accessed online at https://www.geosynthetica.com/wp-content/uploads/Publication243_Durability_C187.pdf.
- 3. “Improving Closure System Performance and Construction Efficiency.” AGRU America. (2020). Accessed online at https://agruamerica.com/our-projects/closure-system-performance/.