The public and media are quick to identify poorly run projects, which are sometimes labeled as bridges to nowhere in reference to projects like the Gravina Island Bridge, which would carry extreme costs at very little benefit. For this reason, government agencies often publish infrastructure reports including cost-benefit analyses to help inform the public about where tax money is going and why. Informational initiatives help draw public support for the most important projects.
One area that is drawing a lot of attention is water infrastructure. Changing climate patterns have forced entire regions in the Unites States to rethink their water strategy. In fact, it will cost about $1 trillion to maintain and expand our water networks to meet demand over the next 25 years, according to the America Water Works Association (AWWA) (1).
Pipe selection is a driving factor behind water infrastructure costs. Below, we will discuss HDPE qualities that affect its long-term durability, explore how these qualities can reduce or even prevent the recurring maintenance costs usually associated with water pipe infrastructure, and describe how larger diameter HDPE pipes can be utilized for additional benefits.
The physical and chemical properties of HDPE promote longevity
High-density polyethylene, or HDPE, is a plastic known for its high strength-to-density ratio, flexibility, and chemical stability making it a perfect choice for pressure and non-pressure piping applications. Typically made with PE100 resin, HDPE pipes will have a density that ranges from 930 to 970 kg/m3, which is about seven times less than steel. A lighter pipe is easier to transport and install. At the same time, HDPE demonstrates high tensile strength and is a non-conductor of electricity. In other words, HDPE is immune to the electrochemical-based corrosion process that is typical during exposure to salts, acids, and bases.
Furthermore, because HDPE pipe’s smooth surface does not corrode and has low friction, the pipe is less susceptible to biological growth and other types of fouling. This resistance to corrosive damage and consistent flow rate means that HDPE pipes have very low maintenance requirements. For improved performance, HDPE pipes can be made with an enhanced resin classified as PE100-RC, which provides for increased resistance to slow crack growth.
When combined with its very long service life, HDPE offers an economic advantage over the entire lifetime of the project.
The economics of HDPE’s longevity
Now that the durability of HDPE has been established, it is important to describe how these properties affect the economics of using HDPE pipes for water infrastructure applications. The most obvious benefit of using HDPE pipes over PVC or ductile iron pipes is leak prevention. There are two types of leaks: Background leakage, which occurs mainly through pipe joints and perforations, and burst failure leakage, which is caused by longitudinal splits and circumferential breaks (1).
The average U.S. utility loses about 14% of its drinking water each day to background leakage—specifically, leaky joints. A city of 100,000 residents with PVC pipe for its water infrastructure would lose about 12,084,785 gallons a year, or about 604,239,250 gallons over the lifetime of the project (2).
The water loss represents not only wasted water and treatment costs, but also the cost of potential infrastructure damage caused by water infiltration (Figure 1). On the other hand, because the joints connecting HDPE pipes can be fusion welded together, AWWA considers the pipe to be “leak-free.” Using HDPE pipes can save cities more than half a billion gallons of water over the lifetime of the pipes. HDPE pipes are also more durable during installation, which means it can support a variety of installation methods including horizontal directional drilling without fear of permanent damage to the pipe.
HDPE pipes sized between OD 1600 mm and up to 3260 mm are now available for large structures
Beyond municipality water systems, large diameter plastic pipe made from HDPE can also be used in desalination and wastewater facilities. Large-diameter, or XXL, HDPE pipes are sized between OD 1600 mm and up to 3260 mm.
There are more than 20,000 desalination facilities around the world and many use HDPE pipes as part of its inflow pipe, with some starting to design XXL sizes (3). The larger flow capacity could also support the water needs of a power plant if the desalination plant is constructed near one. While desalination projects are not yet widespread in the United States due to concerns about startup costs and downtime associated with varied weather patterns (5), wastewater treatment facilities have been in the spotlight since the 1970s.
Wastewater treatment facilities have become an essential component in reducing the environmental impact of infrastructure and human development. To improve the economics of wastewater treatment, most regions prescribe to the joint approach. The joint approach creates specialized wastewater districts where a single treatment facility accepts all the waste from that district’s industrial and municipal operations (6). While there will be many input pipes coming in from municipalities and industrial pretreatment facilities, a single XXL HDPE pipe can be used to feed treated water back into the ocean.
XXL HDPE pipes are well-suited for wastewater treatment applications as they are durable and reliable enough to be buried and left in operation for decades with very few maintenance requirements. The durability of HDPE pipes improves as its size increases, and these pipes have shown incredible seismic resistance. In one case study of the Kobe 1995 earthquake, all other pipes in the city’s infrastructure showed at least one failure every four miles of pipe whereas HDPE pipes demonstrated zero failures across the entire system. XXL HDPE pipes would demonstrate even greater seismic resistance if manufactured with PE100-RC (1).
Summary
While the initial cost of HDPE pipes can be higher than alternative piping materials like PVC, steel, and ductile iron, HDPE pipes provide cost savings by reducing or preventing two types of leaks: background leakage and burst failures.
HDPE’s ability to be fusion welded promotes its zero-leak properties, which can quickly recover its initial higher costs and can lead to added savings over the lifetime of the project. HDPE pipes also offer advantages not seen in other piping solutions such as seismic resistance, which prevents burst failures.
HDPE pipes are well-suited for domestic applications that require the transportation of high volumes of water. Applications include irrigation districts, wastewater treatment facilities, reverse osmosis desalination facilities, and municipalities looking to upgrade its water or sewage systems.
Interested in utilizing HDPE pipe in your next project? Consider AGRU’s HDPE pipes, which can be manufactured at the largest diameters available in North America. Reach out to an AGRU representative or visit our products page for more information.
Figures
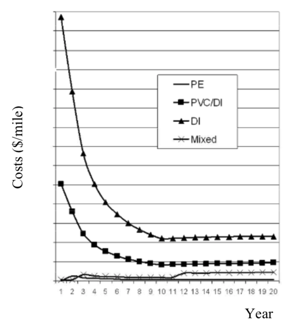
Citations
- Najafi, A. Habibian, and V. F. Sever, “Durability and Reliability of Large Diameter HDPE Pipe for Water Main Applications.” Water Research Foundation. (2015). Accessed online 3 May 2019. http://www.waterrf.org/PublicReportLibrary/4485.pdf.
- Ambrose et al., “Life Cycle Analysis of Water Networks.” Plastic Pipe Institute. Accessed online 3 May 2019. https://plasticpipe.org/pdf/life-cycle-cost-study.pdf.
- “Leakage Calculator.” Alliance for PE Pipes. Accessed online 3 May 2019. http://www.pepipe.org/leakage-calculator.
- “Desalination Worldwide.” Accessed online 3 May 2019. https://www.hbfreshwater.com/desalination-worldwide.html.
- Hiltzik, “Desalination plants aren’t a good solution for California drought.” LA Times. (2015). Accessed online 3 May 2019. https://www.latimes.com/business/hiltzik/la-fi-hiltzik-20150426-column.html.
- S. Watson, “The Advantages of Industrial-Municipal Wastewater Treatment.” Water Poll. Contr. Fed. (1970). Accessed online 3 May 2019. https://www.jstor.org/stable/25036469?seq=1#page_scan_tab_contents.