Leaks and breaks have caused U.S. water utilities to lose more than a quarter of processed water every day as it is transported between treatment plants and the tap. Rehabilitating aging potable water pipes is estimated to cost more than $1 trillion over the next 10 years. Research into these issues shows that there is a need for a reliable and durable pipe material. Results from a 2015 study by the EPA, Water Research Foundation, and the Water Environmental Research Foundation suggests that high-density polyethylene (HDPE) pipe can be the material that meets these requirements (1).
For years, the large diameter (defined as 16 in. and above) water pipe market has been represented in the United States by steel pipe (SP), precast concrete cylinder pipe (PCCP), ductile iron pipe (DIP), and PVC (polyvinyl chloride) pipe. HDPE pipe, on the other hand, comprises just 2 to 5% of the large diameter water pipe market.
This article will summarize the perception issues related to large diameter HDPE pipe as well as recommendations for pipe joining, fittings, specifications, design, installation, and maintenance.
Addressing the misconceptions regarding large diameter HDPE pipes
According to the EPA report, the perception issues surrounding large diameter HDPE pipes come down to three main ideas. First, there is a general lack of knowledge about the product. In a municipality project, the number of stakeholders can complicate the transfer of knowledge about the product to get everyone on the same page. Similarly, workers generally feel more comfortable using familiar products and techniques. Finally, this lack of knowledge can even lead to the misconception that HDPE is unsuitable for water applications.
Even if some knowledge is available, the second perception issue is rooted in the idea that there is an increased risk associated with using novel materials. Users often see HDPE as a new product for their specific application, making it fall outside their comfort zone since there is no experience using it. A significant driver is needed to convince utilities to try new materials and applications. Interesting enough,
The best way to overcome these perception issues is to help quantify perceived risk and demonstrate the quantifiable benefits of using a new material. Additionally, it would be helpful to look at the history of similar products in use. For instance, gas utilities have been using polyethylene pipe since the mid-1960s (2).
Quantifying the benefits of large diameter HDPE pipe
While it is relatively easy to talk about the physical and chemical characteristics of HDPE pipe, a better way to help quantify its benefits is to describe its performance in relation to other piping materials. In a survey conducted with 17 utilities in the United Kingdom, researchers outline the average failure rate from various piping materials. The average failure rate per 62 miles ranged from 20.1 failures on the high end for iron pipes, down to 3.16 failures on the low end for PE pipes. Another interesting finding from this report is that some of the PE utilized in the pipes was manufactured more than 50 years ago. And even the most recent PE pipes in the survey were utilizing the 90s era PE3408, recently superseded by PE4710 and PE 100-RC.
Today, PE manufacturers can manufacture enhanced polymer structures to increase slow crack growth resistance, tensile strength, ductility, allowable hydrostatic stress, and other pipe material properties. The significance of these improvements cannot be overstated. A survey of utilities regarding their satisfaction with PE pipes changed drastically between 1980s and 2000s. While customer satisfaction hovered around 53% during the 1980s, by the 2000s customer satisfaction rose to 95% (see Figure).
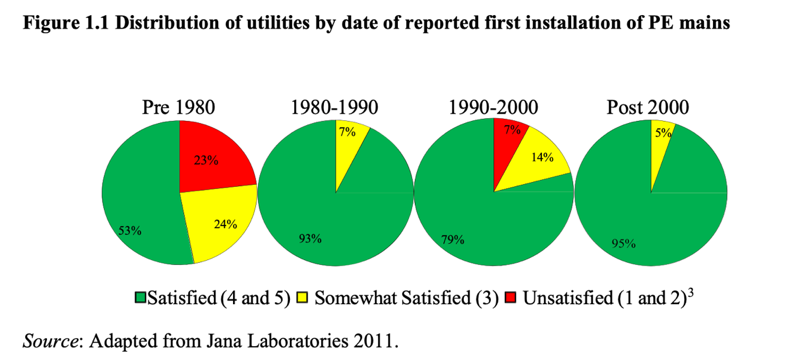
From reference 1.
Large diameter HDPE pipe has been successfully installed in dozens of projects across the United States, including 10 described in the EPA report. The primary reasons quoted for choosing HDPE piping materials for these large diameter transmission mains include flexibility, fusible joints, corrosion resistance, compatibility with trenchless technology methods (e.g., horizontal directional drilling), and cost savings. Ultimately, these benefits were achieved when proper construction methods (especially fusion welding) were followed.
Choosing large diameter (and above) HDPE pipes for municipal piping systems
The EPA report shows that large diameter HDPE pipe is a suitable pipe material for large diameter water transmission applications. The material does not only perform as well as existing piping materials, but also outperforms them in other areas such as seismic resistance, slow-crack growth, failure rates, leakage rates, and more.
AGRU America takes HDPE pipes further by utilizing its decades of experience and superior PE100-RC resin during the manufacturing process. The modified resin offers a number of improvements, the most significant being increased resistance to slow crack growth that allows the pipe to support more intensive installation methods. The stronger resin also allows AGRU to manufacture its pipes in sizes up to OD 3500 mm (described as XXL pipes). Interested in learning more about using large diameter or XXL HDPE pipes in your next municipal or utility project? Reach out to an AGRU representative today.
Learn more
References
- 1. Najafi et al., “Durability and Reliability of Large Diameter HDPE Pipe for Water Main Applications.” Wat. Res. Found. (2015). Accessed online 27 March 2020 at https://www.uta.edu/ce/cuire/4485.pdf.
- 2. “The history of PE pipe.” Hart Energy. (2005). Accessed online 27 March 2020 at https://www.hartenergy.com/news/history-pe-pipe-52531.