Why should you care about concrete protection and restoration?
Thanks to its high strength and low cost, concrete is one of the most widely used construction materials (1). However, it can be subject to various forms of deterioration and damage, including corrosion, abrasion, and chemical exposure, compromising its structural integrity and leading to reduced service life and increased maintenance costs (2–4). For these reasons, it is essential to take protective measures that extend the service life of concrete structures and reduce the need for costly repairs.
Enter concrete protective liner (CPL), an effective solution for protecting and restoring concrete structures (5, 6). CPLs are thin and flexible membranes serving as a barrier to protect the concrete surface from external attacks (7). These liners offer numerous advantages, including ease of installation, cost-effectiveness, and the ability to be customized to fit the shape and size of the concrete structure (fabrication). For these reasons, CPL can be used on most concrete structures, such as bridges, tunnels, water and sewage treatment plants, and industrial facilities. This article explores using CPL for concrete protection and restoration.
Concrete Protective Liners
CPLs have been used for many years in persevering concrete structures by improving their durability and extending their service life. The primary benefit of CPLs for concrete structures is their ability to restore and enhance durability properties, including resistance to abrasion, chemical attacks, and water penetrations (8, 9, 10), at a low cost. An alternative to CPL is spray-on coatings, which are susceptible to backpressure and can wear away in a period far less than the overall service life of the concrete structure.
In addition to corrosion resistance, CPLs can help with thermal insulation (7, 11, 12). However, CPL is most used for internal protection layers in sewer systems’ pipes, acidic attack prevention in tanks, and pile encasements in buildings near the sea (13). CPLs are typically made of polyethylene (PE), high-density polyethylene (HDPE), and polypropylene (PP). Each material offers different advantages when it comes to concrete protection and restoration.
Protecting Concrete with CPL
Water can penetrate reinforced concrete structures through cracks, pores, and other openings due to capillary action when the concrete’s external surface is in direct contact with water or moist substances. Once the water has penetrated the concrete, it causes damage to the reinforcement and other materials within the structure, leading to corrosion and deterioration (Figure 1). Therefore, the concrete element faces deterioration and other aesthetic issues, which can shorten its service life or impact performance.
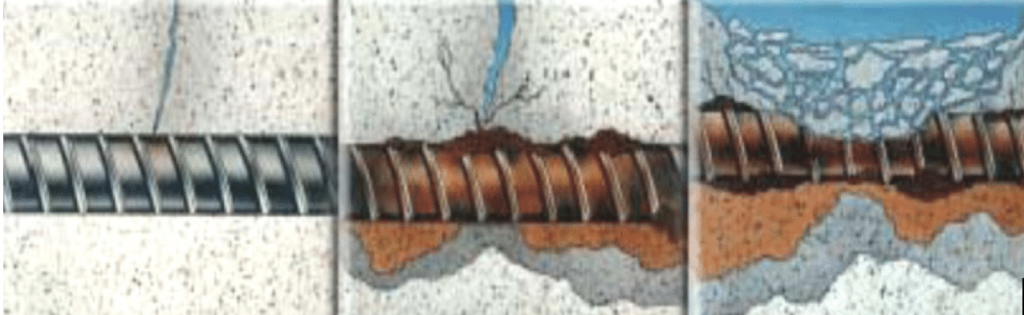
Research studies have demonstrated the effectiveness of using such CPLs to extend the lifespan and reduce the need for costly repairs and maintenance of concrete elements (14). Primarily, CPL is used today to protect concrete structures from corrosion and chemical attacks by providing a barrier that keeps acidic, salt, and other corrosive agents with microbial and biogenetic risks away from the concrete surface (19). These aggressive media are responsible for inducing significant deterioration that reduces the service life of concrete structures (20). Other applications include helping prevent water infiltration for bridge decks (6), parking garages (17), basements (18), tunnels (16), sewer pipes (21), water treatment plants (13), and nuclear waste storage (22).
Besides the purposes mentioned above, CPLs have been used in concrete pipes subjected to heavy abrasions to improve their resistance to wear and tear (15, 23).
Installing CPL
The installation process for CPL depends on the type of liner used, the concrete surface, and whether it is a rehabilitation or new structure. The general process is outlined in Figure 2.

Rehabilitation projects start by cleaning, drying, and ensuring no loose debris or contaminants on the concrete surface. Care should also be taken to repair any visible concrete cracks or holes. After, the liners are measured and cut in the required sizes and shapes while allowing for a slight overlap at the edges. This process is often done with a manufacturer-approved fabricator/installer. Finally, the liners are installed, depending on the product and application, using adhesives, mechanical fasteners, or a combination of both. The edges are then sealed, and the work quality is tested for proper function and against leaks.
For new structures, CPL can line precast concrete structures, including prefabricated concrete elements, concrete pipes and manholes, tank constructions, and oil/water separators. Some CPLs are also specially designed for easy installation within cast-in-situ structures thanks to quick mounting to existing formworks using end profiles and tear-off profiles, as shown in Figure 3. After the concrete sets, the CPL can be extrusion welded to provide a leak-proof solution. This approach enables the installation of both the concrete protective liner and the formwork at the same time. In situ structures include underground construction; foundations and bridges; areas where chemical media are used, transported, or stored; and any basin.
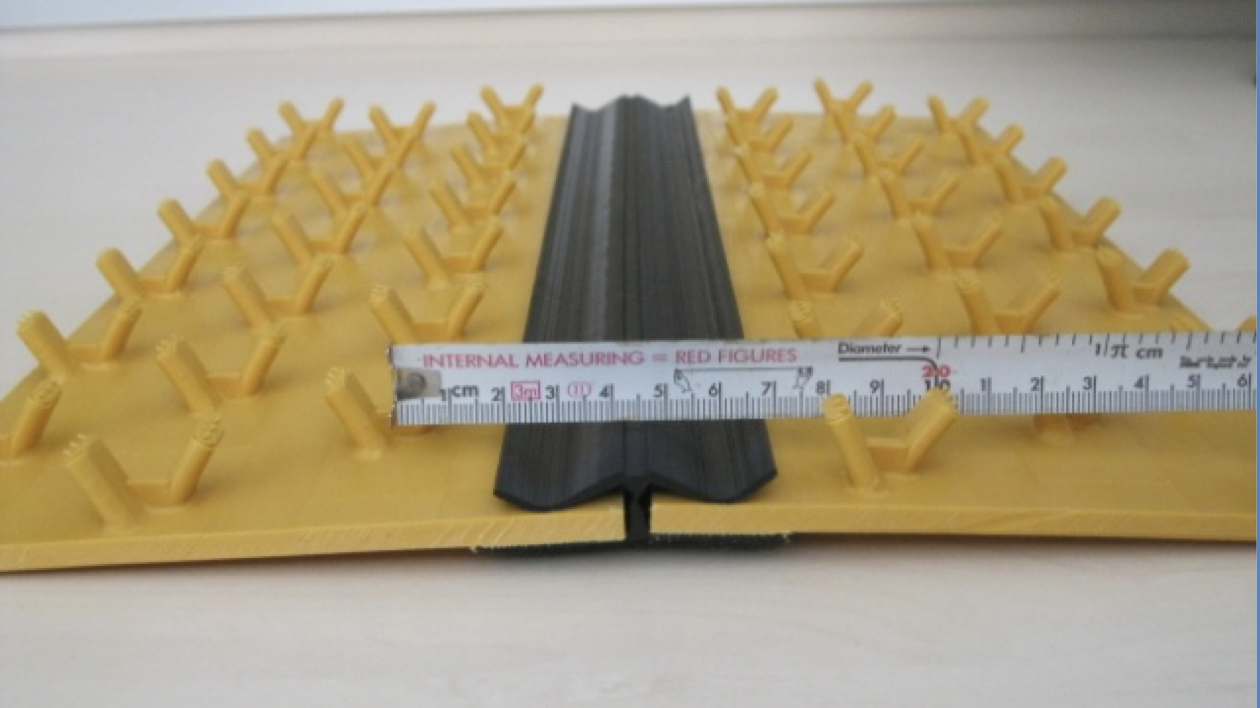
Conclusion: Use CPL for Concrete Protection and Restoration
This study has focused on discussing the applications of concrete protective liners to improve and restore the performance of concrete structures. To summarize:
- CPLs are a versatile and effective solution for protecting and restoring concrete structures as they can be customized to fit the shape and size of the concrete structure and are easy to install.
- CPLs are typically made from various materials, including PP and HDPE. Each material offers beneficial properties that make them well-suited for use as protective liners for concrete structures.
- CPLs are superior waterproofing materials that serve as a protective layer that prevents direct contact between the concrete surface and the liquid environment. As a result, the structure’s durability is improved, improving service life at a lower cost.
- CPLs are resistant to abrasion and chemicals and have good thermal insulation properties.
AGRU offers over 30 years of experience producing concrete protective liners (CPL) and leads the industry with innovations, including AGRU-ULTRA GRIP® with a revolutionary redesign of the 13 mm Sure-Grip anchor.
Ultra Grip, produced from high-density polyethylene (HDPE) and polypropylene (PP), is available in various colors and configurations for both rolls and sheets and is among the widest CPL produced in the United States at 10 feet. But its exceptional backpressure resistance sets Ultra-Grip apart from competitors.
Want to learn more about AGRU CPL for concrete protection and restoration?
Learn More
References
(1) M. Singh et al. “A study on environmental and economic impacts of using waste marble powder in concrete.” Journal of Building Engineering. (2017).
(2) C. Maraveas. “Durability issues and corrosion of structural materials and systems in farm environment.” Applied Sciences. (2020).
(3) S. W. Tang et al. “Recent durability studies on concrete structure.” Cement and Concrete Research. (2015).
(4) M. Albitar et al. “Durability evaluation of geopolymer and conventional concretes.” Construction and Building Materials. (2017).
(5) F. Mazzotta et al. “Performance evaluation of recycled rubber waterproofing bituminous membranes for concrete bridge decks and other surfaces.” Construction and Building Materials. (2017).
(6) Q. Zhou and Q. Xu. “Experimental study of waterproof membranes on concrete deck: Interface adhesion under influences of critical factors.” Materials & Design. (2009).
(7) P. C. Hewlett. “Methods of protecting concrete—coatings and linings.” Protection of Concrete: Proceedings of the International Conference. (1990).
(8) B. Shojaei et al. “A review on the applications of polyurea in the construction industry.” Polymers for Advanced Technologies. (2021).
(9) M. Sánchez et al. “External treatments for the preventive repair of existing constructions: A review.” Construction and Building Materials. (2018).
(10) A. K. Parande et al. “Deterioration of reinforced concrete in sewer environments.” Proceedings of the Institution of Civil Engineers-Municipal Engineer. (2006).
(11) P. A. Schweitzer. “Corrosion-resistant linings and coatings.” CRC press. (2001).
(12) G. A. Whyatt and R. K. Farnsworth. “The high pH chemical and radiation compatibility of various liner materials.” Geosynthetic Testing for Waste Containment Applications. (1990).
(13) P. G. Dimaio. “Introduction to Concrete Protection Liners.” Geo-Frontiers 2011: Advances in Geotechnical Engineering. (2011).
(14) N. Z. Muhammad et al. “Waterproof performance of concrete: A critical review on implemented approaches.” Construction and Building Materials. (2015).
(15) T. Abel and N. Pelczar. “Modern concrete pipes: a review of reinforcement and new technologies.” Studia Geotechnica et Mechanica. (2021).
(16) D. R. Chapman. “Selection and design of corrosion protection liner for precast concrete segment tunnel liner.” In North American Tunneling 2002. (2021).
(17) G. G. Litvan. “Waterproofing of parking garage structures with sealers and membranes: the Canadian experience.” Construction and Building Materials. (1996).
(18) Z. Bonić et al. “Some methods of protection of concrete and reinforcment of reinforced-concrete foundations exposed to environmental impacts.” Procedia Engineering. (2015).
(19) B. Chaudhari et al. “Microbiologically Induced Concrete Corrosion: A Concise Review of Assessment Methods, Effects, and Corrosion-Resistant Coating Materials.” Materials. (2022).
(20) R. P. George et al. “Current understanding and future approaches for controlling microbially influenced concrete corrosion: a review.” Concrete research letters. (2012).
(21) C. W. Fourie. “Acid resistance of sewer pipe concrete.” University of Cape Town. (2007).
(22) R. T. Anderson and S. Pearson. “Integration of Low-Level Nuclear Waste Storage and Disposal Requirements in the 1990s.” WASTE MANAGEMENT-TUCSON. (1993).
(23) G. DeCou and P. Davies. “Evaluation of abrasion resistance of pipe and pipe lining materials (No. FHWA/CA/TL¿ CA01-0173).” California. Dept. of Transportation. (2007).