What are DIPS HDPE pipes, and why are they significant? This article will give context to ductile iron pipe size (DIPS) for high-density polyethylene (HDPE) pipes based on published history and the expert opinion of Harvey Svetlik, P.E., an industry veteran with over 40 years of experience and a mainstay across numerous committees including AWWA, ASTM, NACE, and FM.
Water’s efficient management and distribution have underpinned societal growth and development since the beginning of civilization (1). The need for robust, sustainable, and efficient water distribution systems has driven significant technological and institutional improvements (2). For example, how we convey water has transitioned from rudimentary aqueducts of ancient civilizations to today’s highly sophisticated underground piping systems (3).
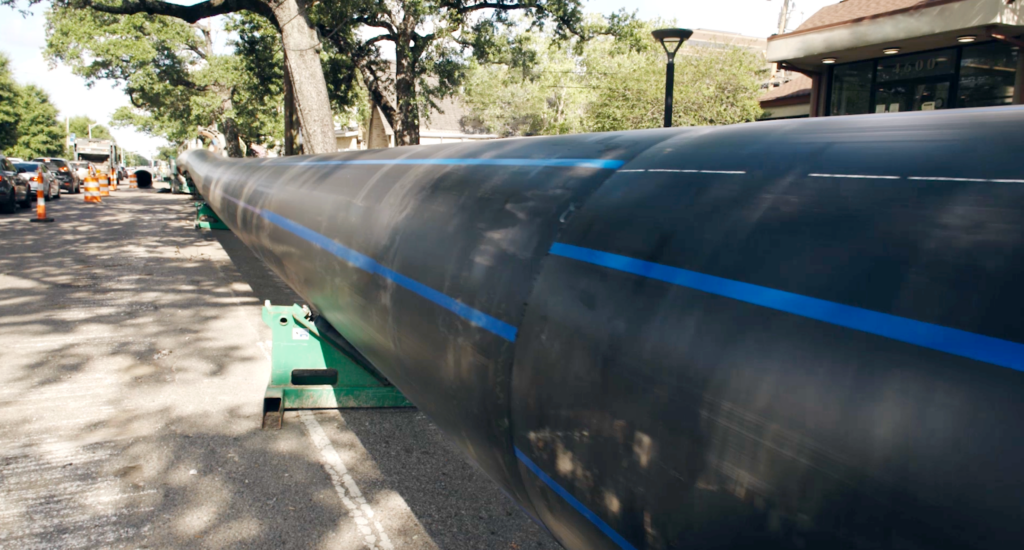
Modern water distribution systems rely on selecting appropriate materials and sizes according to application (4). With plastic pipes, specifically HDPE, several sizing terms have been used to mirror the materials and designs that were once the traditional choices. Here, we explore the history and evolution of DIPS HDPE pipes and their significance.
Evolution of DIPS Pipes
During the 17th century, cast-grey-iron outside diameter (CIOD) pit-cast pipes dominated the piping industry (5). The 20th century saw innovations in material sciences and engineering, which helped develop the concept of ductile iron spin-cast iron pipes. By the mid-20th century, polyvinyl chloride (PVC) pipes began to emerge, representing a shift in the material preference toward polymers (6). During this era, most cities leaned heavily on cast iron pipes to distribute water (7). As these networks expanded to include polymers, the need for a standardized sizing system arose, leading to the development of new standards.
“With polyethylene’s 25 years of performance at the time, we saw an opportunity to build standards around this advanced polymer,” said Mr. Svetlik. In 1992, the DIPS was coined, starting a new chapter in the piping industry as engineers began turning to HDPE for more projects. Since then, the material has provided another 30 years of exceptional performance.
«The DIPS term ensured that HDPE would be differentiated from the PVC CIOD pipes while maintaining sizing close to that of ductile iron pipe,» said Mr. Svetlik. According to Mr. Svetlik, the term was crucial to support the creation of standards like AWWA C906, which were in part composed to set guidelines for HDPE pipes compared with the established norms for ductile iron pipes (8).
“With polyethylene’s 25 years of performance at the time, we saw an opportunity to build standards around this advanced polymer,”
Harvey Svetlik
The three main ways to measure HDPE pipes are iron pipe size (IPS), DIPS, and metric. Each has its specific uses. For IPS and DIPS, the choice often comes down to interoperability with existing systems. There are also operational differences.
“A notable characteristic of DIPS is their larger inside diameter, increased flow, and reduced back pressure,” said Mr. Svetlik. These features make DIPS HDPE pipes attractive to municipalities, which often rely on gravity flow from elevated tanks rather than active pumps for water distribution (9, 10). This means that while the source raw water might be pumped to treatment plants, post-treatment distribution depends on gravity (11). Thus, the broader inside diameter of DIPS pipes facilitates this gravity-driven flow, ensuring efficient water delivery.
DIPS Adoption and Adaptation
Today, the significance of DIPS extends beyond its dimensions. With DIPS as a standardized sizing system, integrating new sections into existing networks is far more manageable. As a result, using DIPS has allowed for new, seamless connections in many municipalities with legacy ductile iron piping systems (12).
“DIPS HDPE pipes enable interoperability with existing ductile iron pipe infrastructure,” said Mr. Svetlik. This is important since our aging infrastructure relies on rehabilitation, often through various means. Additionally, interoperability has become a deciding factor in material and design choices to meet the demand for growing cities (13). “In other words, with DIPS HDPE pipes, you can expect support and access to a full suite of fittings, adaptors, and maintenance and repair products that have been used in ductile iron piping systems for decades,” said Mr. Svetlik.
DIPS HDPE pipes are also ideal for trenchless technologies, supporting horizontal directional drilling (HDD), slip lining, compressed fit, and other modern installation techniques.
Beyond water distribution, the DIPS’s consistent dimensions made it a favored choice for policymakers in applications related to other fluid distribution systems, including wastewater, reclaimed water, and stormwater management (14). The expansion of DIPS HDPE pipes into these sectors highlighted its adaptability and underscored its value as a solution for various water transmission problems. Another notable real-life application where DIPS was used was rehabilitating a 36-inch abandoned concrete cylinder pipe in the Sahuarita Slipliner Project (15).
DIPS HDPE Pipes in Action
With ASTM F3508, engineers have a method to rehabilitate existing infrastructure (the host pipe) called compressed fit. This method works by radially reducing a new polymer pipe like HDPE, pulling/pushing it through the host pipe, and then allowing it to expand to press against the inside diameter of the host pipe. The result couples the interior pipe to reinforce the host pipe, restoring leak tightness and adding strength to the host pipe. According to the standard, these reconstructed pipelines or conduits are suitable for both pressure and non-pressure pipeline applications such as process piping, raw and treated water transmission, water pipe systems, forced mains, industrial and oil-patch gathering and transmission pipelines, sanitary sewers, storm sewers, and culverts.
HDPE pipes allow engineers to leverage their properties to tackle unique challenges or geographical limitations. HDPE pipes offer remarkable flexibility, while their internal and external corrosion resistance ensures longevity, even in environments detrimental to other materials (See Table 1; 16, 17). These advantages have resulted in an excellent satisfaction rate, as shown in Figure 1 (18). The smooth interior of HDPE pipes also ensures low internal friction, promoting efficient fluid flow. Another notable feature is that the material supports butt-fused connections, establishing a continuous, jointless pipeline that virtually eliminates leakage.
Benefits of HDPE Pipes | Description/Details |
Longevity | HDPE pipes can last in excess of 100 years under most conditions. |
Chemical Resistance | HDPE pipes are resistant to chemical attack by strong oxidizers. They contain additives protecting them from the oxidizing effects of disinfectants. |
Safety Factor | Anticipates and accounts for water hammer, allowing for surges up to 1.5 times the pipe’s pressure class and occasional surges up to two times the pressure class. |
Temperature Resilience | The working pressure rating of HDPE pipe is maintained for temperatures up to 80°F and can be used up to a maximum of 100°F with compensation. |
Flexibility | Especially during seismic events, HDPE pipes have fewer failures as compared to other materials. |
Low Leakage Cost | HDPE pipe has the lowest leakage cost when compared to PVC/DI, DI, and mixed pipe materials. |
Leak-Proof Joints | Fused joints in HDPE pipes eliminate leaks at the pipe joints, leading to zero allowable water leakage. |
Resistance to SCG | Modern bimodal HDPE polymer is virtually inert to slow crack growth (SCG). Besides, PE4710 resin and pipe standards have test requirements that validate that resistance to SCG. |
Furthermore, these pipes exhibit abrasion resistance, while their high ductility, flexibility, and lightweight nature allow for efficient installations (16, 19, 20). HDPE’s inherent resistance to fatigue, recurring surge pressures, earthquakes, and impacts at extremely low temperatures make it a durable option for sustainable infrastructure (21). Finally, in the unlikely event of damage, these pipes can be seamlessly repaired using various methods, including mechanical couplings, fusion, and electrofusion. These benefits underscore the versatility and resilience of HDPE pipes.
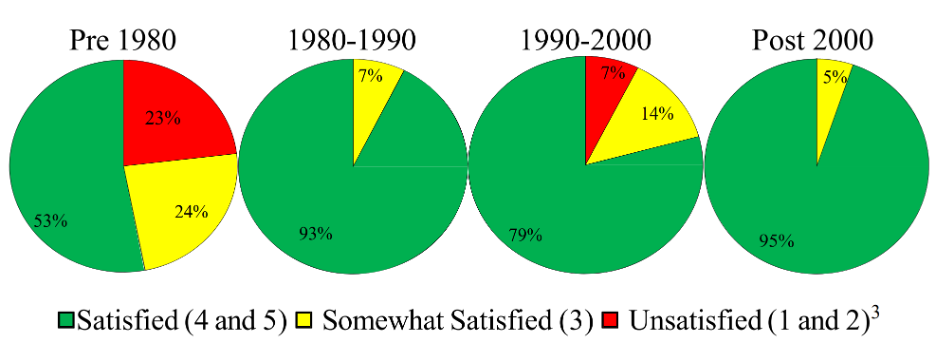
In New Orleans, DIPS HDPE pipes have become essential for the city’s future. Hurricane Katrina affected much of the city’s infrastructure and is on record as the costliest storm at ~$193 billion in damage, adjusted to 2023. The storm coincided with many boil orders as untreated stormwater overwhelmed systems and entered the water main. To rectify these issues, the Sewerage & Water Board of New Orleans launched an 11-project effort in 2023 to replace its 100- to 120-year-old water transmission mains with a modern piping system.
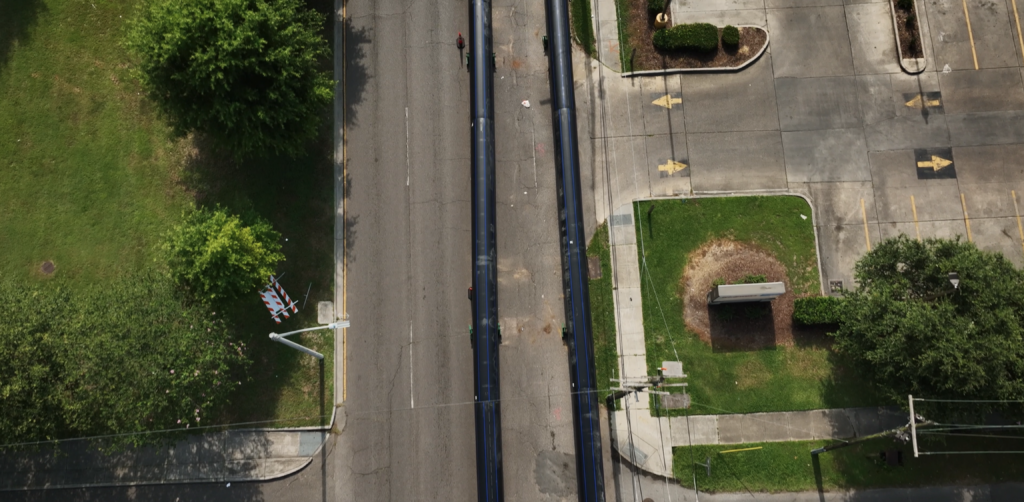
The South Claiborne Transmission Main Project, one of the 11 projects in New Orleans, aimed to stabilize water pressure in many parts of the city, improve water quality, and allow for long-term repairs for roadways and pavements. The project relied on the compressed fit installation method. For that to work, the project required some of the largest DIPS HDPE pipes ever made in the United States. Over 5,600 ft of 30” and 48” DIPS SDR 17 HDPE pipes were manufactured in the United States by AGRU.
The installers were able to finish this project in record time and minimize disruption to the public. Additionally, the project owners estimate about a 25% cost savings thanks to the installation method. Read more about this case study.
Conclusion
Establishing DIPS HDPE pipes as a system has been pivotal in shaping how municipalities modernize their water distribution systems thanks to its focus on inside diameter, its working pressure ratings matched to system operating pressure, interoperability with existing ductile iron piping systems, and its ability to withstand surge. With more manufacturers offering DIPS HDPE pipes, engineers have even more ways to rehabilitate existing piping systems thanks to compressed fit.
Are you considering HDPE pipes for your next project? Work with AGRU’s technical experts to assist with project feasibility and help you find certified distributors and installers for AGRULINE’s IPS, DIPS, and metric options.
Review Datasheet
References
(1) D. Zilberman et al. «Efficient management of water in agriculture.» Efficient management of water in agriculture. Decentralization and coordination of water resource management. (1997).
(2) J. G. Hering et al. «A Changing Framework for Urban Water Systems.» Environmental Science & Technology. (2013).
(3) T. M. Walski. «A history of water distribution.» J. AWWA. (2006).
(4) L. W. Mays. «Water distribution system handbook.» McGraw-Hill Education. (2000).
(5) «Ductile iron pipe systems.» EADIPS FGR. (2018).
(6) R. B. Seymour, «Plastic Pipe for Underground Structures.» Corrosion. (1955).
(7) A. B. Paradkar. «An Evaluation of Failure Modes for Cast Iron and Ductile Iron Water Pipes.» (2013).
(8) «AWWA C906-15 Polyethylene (PE) Pressure Pipe and Fittings. 4 In. Through 65 In. (100 mm Through 1.650 mm). for Waterworks.» AWWA. (2021).
(9) T. Marti. «Setting the Record Straight—ISO S4 Testing for AWWA C900 Pipe.» (2015).
(10) A. De Corte and K. Sörensen. «Optimisation of gravity-fed water distribution network design: A critical review.» European Journal of Operational Research. (2013).
(11) «Gravity-flow water systems.» WaterAid. (2021).
(12) «PE Pipe Design and Installation: M55 (Vol. 55).» AWWA. (2006).
(13) M. Salinas and J. Garcia. «Up for Rehab: Proactive Pipeline Rehabilitation to Prevent Failure in SAWS’Largest Lift Station.» Pipelines. (2023).
(14) «Uniform Water. Wastewater. And Reclaimed Water Systems Code.» Sarasota County, Florida. (2011).
(15) K. L. Miller. «Sahuarita Slipliner Project.» Pipelines. (2017).
(16) K. Q. Nguyen et al. «Long-term testing methods for HDPE pipe-advantages and disadvantages: A review.» Engineering Fracture Mechanics. vol. 246. p. 107629. (2021).
(17) F. R. Rofooei et al. «Parametric study of buried steel and high-density polyethylene gas pipelines due to oblique-reverse faulting.» Canadian Journal of Civil Engineering. vol. 42. no. 3. pp. 178-189. (2015).
(18) J. Laboratories. «Polyethylene (PE) Pipe Performance in Potable Water Distribution Systems; Past. Present and Future.» (2011).
(19) K. Peterson. «HDPE pipe for corrosion-and leak-free operation.» ASHRAE Journal. vol. 59. no. 7. pp. 54-59. (2017).
(20) G. DeCou and P. Davies. «Evaluation of abrasion resistance of pipe and pipe lining materials.» California Department of Transportation. (2007).
(21) C. G. Rubeiz. «Case studies on the use of HDPE pipe for municipal and industrial projects in North America,» Pipeline Engineering and Construction: What’s on the Horizon? (2004).
(22) «Durability and Reliability of Large Diameter HDPE Pipe for Water Main Applications.» Water Research Foundation. (2015).